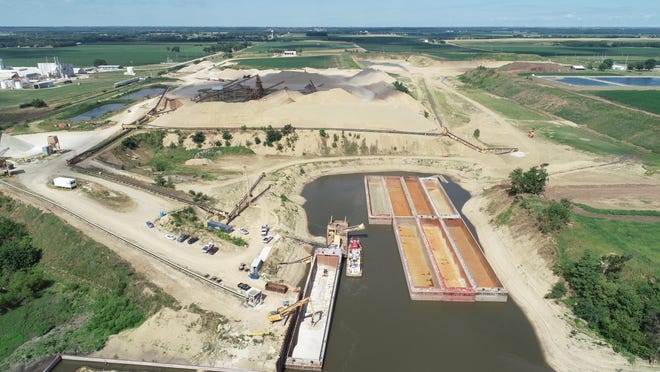
A company must satisfy 14 elements in order for it to be considered PSM. These elements are Process hazard analysis, Permissible exposure limits and Physical data. These elements are crucial to the success of a PSM Program. Compliance will be achieved if the company adheres to these elements. The following sections will detail these elements and how they should be applied to your company.
Analyses for process hazards
An essential element of any safety management program is the process hazard analysis. It helps to identify potential hazards and assess the consequences of failure. This analysis must be done with a group of people who are familiar with the process. This analysis will consider human factors, previous incidents, and review the location of the facility. The analysis must be reviewed every five years after it is completed. As part of a safety management program, the process of hazard analysis must also be implemented.
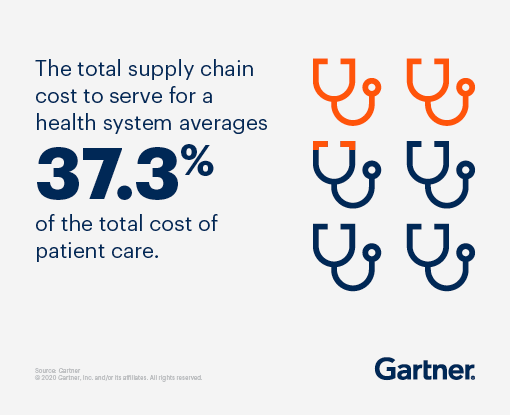
Permissible exposure limits
OSHA Process Safety Management is a set standard for hazardous chemical, gas, or liquid processes. The standard applies to all businesses that produce or process hazardous chemical products. It does not cover hydrocarbon fuels used exclusively for workplace use, retail or well drilling. It does not apply to facilities that are normally vacant or remote.
Physical data
PSM is the process of analyzing and controlling the risk of hazardous materials and products. This entails understanding how to safely handle, transport, and store hazardous substances. This will result in less product waste and fewer workplace injuries. It makes it easier to make decisions and allows organizations to prioritize safety and health. PSM is a vital part of a safe workplace. It is also a cost-saving tool that helps businesses avoid medical emergencies.
Data on corrosivity
The PSM standard specifies requirements for the handling and storage of chemicals and other substances that can cause damage to buildings and equipment. The PSM standard also requires periodic compliance audits. PSM-compliant workplaces will provide safety and protection for employees, no matter how hazardous your organization's production processes are.
Data about thermal stability
OSHA has developed a standard for collecting and reporting PSM thermal stability data. Researchers will be able to identify potential hazards and minimize the consequences of accidental releases. It will be updated regularly to reflect new research tasks. It will be made available to all employees. The PSM program contains information on toxicity, corrosion, and physical property.
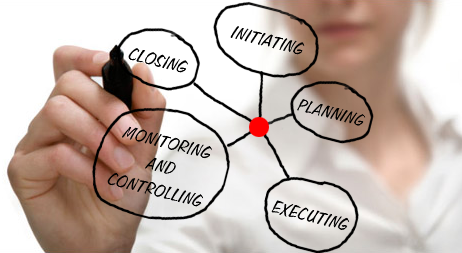
Participation clause
Process Safety Management (PSM), a systematic approach to the prevention and control of hazardous chemicals (HHC)-related process accidents, is an analytical approach. It is a crucial step in improving safety at work and must be applied at all levels of the plant. It has 14 elements that must be implemented, including clauses for employee participation. Here are some examples of elements and requirements.
FAQ
What is a simple management tool that aids in decision-making and decision making?
A decision matrix, a simple yet powerful tool for managers to make decisions, is the best. It allows them to consider all possible solutions.
A decision matrix represents alternatives in rows and columns. This allows one to see how each alternative impacts other options.
We have four options in this example. They are represented by the boxes to the left of the matrix. Each box represents an alternative. The top row displays the current situation, and the bottom row shows what might happen if nothing is done.
The effect of Option 1 can be seen in the middle column. In this case, it would mean increasing sales from $2 million to $3 million.
These are the results of selecting Options 2 or 3. These positive changes can increase sales by $1 million or $500,000. But, they also have some negative consequences. Option 2, for example, increases the cost by $100 000 while Option 3 decreases profits by $200 000.
The last column displays the results of selecting Option 4. This involves decreasing sales by $1 million.
The best thing about a decision matrix is the fact that you don't have to remember which numbers go with what. You can just glance at the cells and see immediately if one given choice is better.
The matrix has already done all of the work. It is as simple a matter of comparing all the numbers in each cell.
Here is an example of how a decision matrix might be used in your business.
You want to decide whether or not to invest more money into advertising. By doing so, you can increase your revenue by $5 000 per month. You will still have to pay $10000 per month in additional expenses.
The net result of advertising investment can be calculated by looking at the cell below that reads "Advertising." It is 15 thousand. Advertising is more valuable than its costs.
What is Kaizen?
Kaizen is a Japanese term for "continuous improvement." It encourages employees constantly to look for ways that they can improve their work environment.
Kaizen is built on the belief that everyone should be able do their jobs well.
What is the difference between Six Sigma Six Sigma and TQM?
The main difference between these two quality management tools is that six sigma focuses on eliminating defects while total quality management (TQM) focuses on improving processes and reducing costs.
Six Sigma can be described as a strategy for continuous improvement. It emphasizes the elimination and improvement of defects using statistical methods, such as control charts, P-charts and Pareto analysis.
This method attempts to reduce variations in product output. This is accomplished by identifying the root cause of problems and fixing them.
Total Quality Management involves monitoring and measuring every aspect of the organization. It also involves training employees to improve performance.
It is used to increase productivity.
What is Six Sigma?
It's a strategy for quality improvement that emphasizes customer care and continuous learning. The goal is to eliminate defects by using statistical techniques.
Six Sigma was developed at Motorola in 1986 as part of its efforts to improve manufacturing processes.
The idea quickly spread in the industry. Many organizations today use six-sigma methods to improve product design and production, delivery and customer service.
How do you effectively manage employees?
Effectively managing employees means making sure they are productive and happy.
This also involves setting clear expectations and monitoring their performance.
Managers need clear goals to be able to accomplish this.
They should communicate clearly with employees. They also need to make sure that they discipline and reward the best performers.
They must also keep track of the activities of their team. These include:
-
What was accomplished?
-
How much work were you able to accomplish?
-
Who did it?
-
It was done!
-
Why did it happen?
This information can help you monitor your performance and to evaluate your results.
What is the difference between a project and a program?
A project is temporary; a program is permanent.
Projects usually have a goal and a deadline.
It is often carried out by a team of people who report back to someone else.
A program will usually have a set number of goals and objectives.
It is usually implemented by a single person.
Statistics
- Your choice in Step 5 may very likely be the same or similar to the alternative you placed at the top of your list at the end of Step 4. (umassd.edu)
- This field is expected to grow about 7% by 2028, a bit faster than the national average for job growth. (wgu.edu)
- Hire the top business lawyers and save up to 60% on legal fees (upcounsel.com)
- The average salary for financial advisors in 2021 is around $60,000 per year, with the top 10% of the profession making more than $111,000 per year. (wgu.edu)
- The profession is expected to grow 7% by 2028, a bit faster than the national average. (wgu.edu)
External Links
How To
How can you implement Quality Management Plan (QMP).
The Quality Management Plan (QMP) was established in ISO 9001. It is a systematic way to improve processes, products and services. It focuses on the ability to measure, analyze and control processes and customer satisfaction.
QMP stands for Quality Management Process. It is used to guarantee good business performance. QMP is a standard method that improves the production process, service delivery, customer relationship, and overall business performance. QMPs must include all three elements - Products, Services, and Processes. When the QMP includes only one aspect, it is called a "Process" QMP. When the QMP focuses on a Product/Service, it is known as a "Product" QMP. QMP stands for Customer Relationships.
Scope, Strategy and the Implementation of a QMP are the two major elements. They can be described as follows:
Scope: This describes the scope and duration for the QMP. This will be used to define activities that are performed in the first six months of a QMP.
Strategy: These are the steps taken in order to reach the goals listed in the scope.
A typical QMP is composed of five phases: Planning Design, Development, Implementation and Maintenance. Each phase is described below:
Planning: This stage identifies and prioritizes the QMP's objectives. All stakeholders involved in the project are consulted to understand their requirements and expectations. After identifying the objectives, priorities and stakeholder involvement, it's time to develop the strategy for achieving the goals.
Design: During this stage, the design team develops the vision, mission, strategies, and tactics required for the successful implementation of the QMP. These strategies are then put into practice by creating detailed plans.
Development: Here, the development team works towards building the necessary capabilities and resources to support the implementation of the QMP successfully.
Implementation: This is the actual implementation and use of the QMP's planned strategies.
Maintenance: Maintaining the QMP over time is an ongoing effort.
Several additional items should be added to the QMP.
Stakeholder Involvement: Stakeholders are important for the success of the QMP. They should actively be involved during the planning and development, implementation, maintenance, and design stages of QMP.
Project Initiation - A clear understanding of the problem statement, and the solution is necessary for any project to be initiated. In other words, they must understand the motivation for initiating the project and the expectations of the outcome.
Time frame: The QMP's timeframe is critical. The simplest version can be used if the QMP is only being implemented for a short time. For a long-term commitment you may need more complicated versions.
Cost Estimation - Cost estimation is an important part of the QMP. You can't plan without knowing how much money it will cost. The QMP should be cost-estimated before it can begin.
QMPs are more than just documents. They can also be updated as needed. It changes as the company grows. It is important to review it periodically to ensure it meets all current requirements.