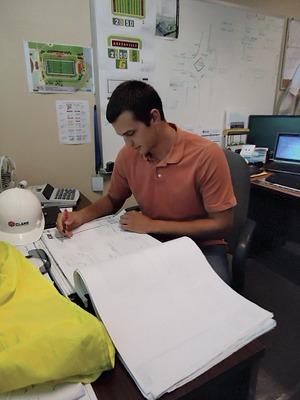
Logistics is the movement and storage of goods from production to delivery. Logistics involves many people, organizations, activities, information, and companies that make goods available for sale. A logistics supply network is a collaborative effort of multiple stakeholders. Although logistics is the main focus of many companies' operations, the process can incorporate other components such as transport and software. These are some of the various types of logistical systems. Read on to learn more about these systems and how they can improve your company's supply chain operations.
Logistics is the movement, storage, and distribution of goods from initial production to final delivery
Logistics involves the efficient movement and storage of products from initial production to final delivery. If flows are optimized, products reach the customers at just the right time, at exactly the right location, and at the perfect cost. These seven "rights of logistics" are listed below. The first is getting it right. Products should be delivered to customers on time, without delay, in the right condition.
Inbound logistics concentrates on the inbound movement materials and products to manufacturers. While outbound logistics focuses more on the outbound flow goods and information from outside sources, Inbound logistic focuses on the acquisition of materials and the arrangement for inbound transportation, storage, delivery, and distribution to customers. Reverse logistic deals with return shipment of finished goods and their packaging. Some cases may include reusable packaging and disposal.
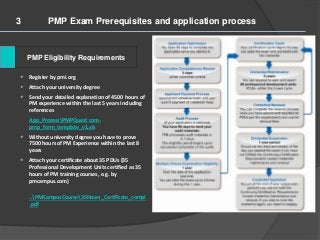
It is an ad-hoc business.
A risk-adjusted investor (RAR) is a type of investment that involves capital or funds that are more risky than normal business investments. The opportunity cost or risk is the difference in return on risk-adjusted investments from normal business investments. RAR can reduce investment risk and assist business owners in managing cash flows across different business functions.
It is just a part of a larger, more collaborative supply chain
A highly integrated supply system is a network of suppliers that are interdependent and rely on prompt delivery of quality components. In such a chain, failure to deliver could bring the whole chain to a halt. Every disruption can be prevented by even the most reliable suppliers and logistic providers. Each participant must assess the risks to the system to ensure the overall chain is efficient and smooth.
Collaborations between manufacturers and retailers can have a positive impact on both parties. For example, a recent collaboration between a retailer and a large U.S. retail chain resulted in a reduced logistics cost between the factory and the store. Retailers can increase their sales by collaborating in this area. To reduce transport and labor costs between factory and store, manufacturers and retailers can work together.
It involves software
Software that manages supply chains can be used to help companies. The software manages all aspects of the supply chains, from vendor relationships to transactions. Supply chain management software can be used by any size business. These software programs allow you to manage your inventory, supplier relationships, as well as the flow of data throughout your organization. These programs may cover all stages in product development, including shipping and warehousing. These programs may include inventory management and insight on trends and customer demand.
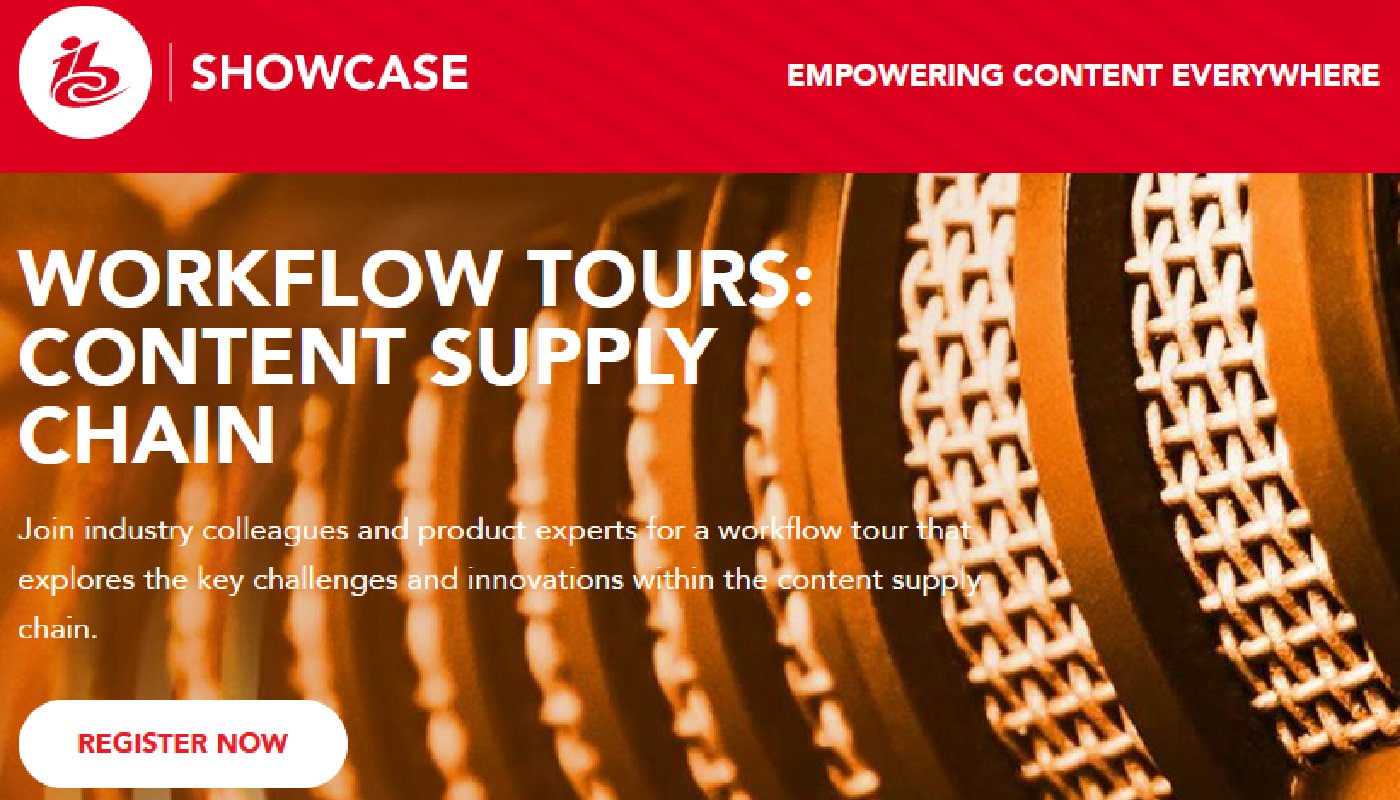
Software for logistics management can improve inventory management, real time fleet management, and streamline communication. It can also improve customer services. It automates everyday tasks and provides actionable insights to business owners. It improves communication and inventory processes which are essential to the success of supply chain management. These applications can help you improve customer service and increase profitability. You might be curious about the benefits of purchasing software for your business.
FAQ
What is TQM?
The industrial revolution was when companies realized that they couldn't compete on price alone. This is what sparked the quality movement. They needed to improve quality and efficiency if they were going to remain competitive.
Management developed Total Quality Management to address the need for improvement. It focused on all aspects of an organisation's performance. It included continuous improvement, employee involvement and customer satisfaction.
What is the difference in a project and program?
A project is temporary, while a program lasts forever.
A project has usually a specified goal and a time limit.
It is often done in a team that reports to another.
A program typically has a set goal and objective.
It is usually implemented by a single person.
What is Six Sigma and how can it help you?
It's a strategy for quality improvement that emphasizes customer care and continuous learning. The goal is to eradicate defects through statistical techniques.
Motorola created Six Sigma as part of their efforts to improve manufacturing processes in 1986.
It was quickly adopted by the industry and many companies are now using six-sigma to improve product design, production, delivery, customer service, and product design.
What are the 4 major functions of management
Management is responsible in planning, organizing and directing people and resources. It also includes developing policies and procedures and setting goals.
Management assists an organization in achieving its goals by providing direction, coordination and control, leadership, motivation, supervision and training, as well as evaluation.
These are the four major functions of management:
Planning - Planning refers to deciding what is needed.
Organizing – Organizing means deciding how to organize things.
Directing - Directing is when you get people to do what you ask.
Controlling - This is the ability to control people and ensure that they do their jobs according to plan.
What are management theories?
Management concepts are the principles and practices used by managers to manage people, resources. They include such topics as human resource policies, job descriptions, performance evaluations, training programs, employee motivation, compensation systems, organizational structure, and many others.
How can a manager improve his/her managerial skills?
You can improve your management skills by practicing them at all times.
Managers need to monitor their subordinates' performance.
It is important to take immediate action if your subordinate doesn't perform as expected.
You should be able to identify what needs improvement and how to improve things.
Statistics
- Our program is 100% engineered for your success. (online.uc.edu)
- As of 2020, personal bankers or tellers make an average of $32,620 per year, according to the BLS. (wgu.edu)
- The average salary for financial advisors in 2021 is around $60,000 per year, with the top 10% of the profession making more than $111,000 per year. (wgu.edu)
- Your choice in Step 5 may very likely be the same or similar to the alternative you placed at the top of your list at the end of Step 4. (umassd.edu)
- Hire the top business lawyers and save up to 60% on legal fees (upcounsel.com)
External Links
How To
How do I do the Kaizen Method?
Kaizen means continuous improvement. This Japanese term refers to the Japanese philosophy of continuous improvement that emphasizes incremental improvements and constant improvement. It's where people work together in order to improve their processes constantly.
Kaizen is one method that Lean Manufacturing uses to its greatest advantage. In this concept, employees who are responsible for the production line must identify problems that exist during the manufacturing process and try to solve them before they become big issues. This increases the quality of products and reduces the cost.
Kaizen is about making everyone aware of the world around them. So that there is no problem, you should immediately correct it if something goes wrong. If someone is aware of a problem at work, he/she should inform his/her manager immediately.
There are some basic principles that we follow when doing kaizen. Always start with the end product in mind and work our way back to the beginning. If we want to improve our factory for example, we start by fixing the machines that make the final product. Then, we fix the machines that produce components and then the ones that produce raw materials. And finally, we fix the workers who work directly with those machines.
This is known as "kaizen", because it emphasizes improving each step. After we're done with the factory, it's time to go back and fix the problem.
Before you can implement kaizen into your business, it is necessary to learn how to measure its effectiveness. There are several ways to determine whether kaizen is working well. Another way to determine if kaizen is working well is to look at the quality of the products. Another method is to determine how much productivity has improved since the implementation of kaizen.
A good way to determine whether kaizen has been implemented is to ask why. It was because of the law, or simply because you wanted to save some money. You really believed it would make you successful?
Let's say you answered yes or all of these questions. Congratulations! You're ready to start kaizen.