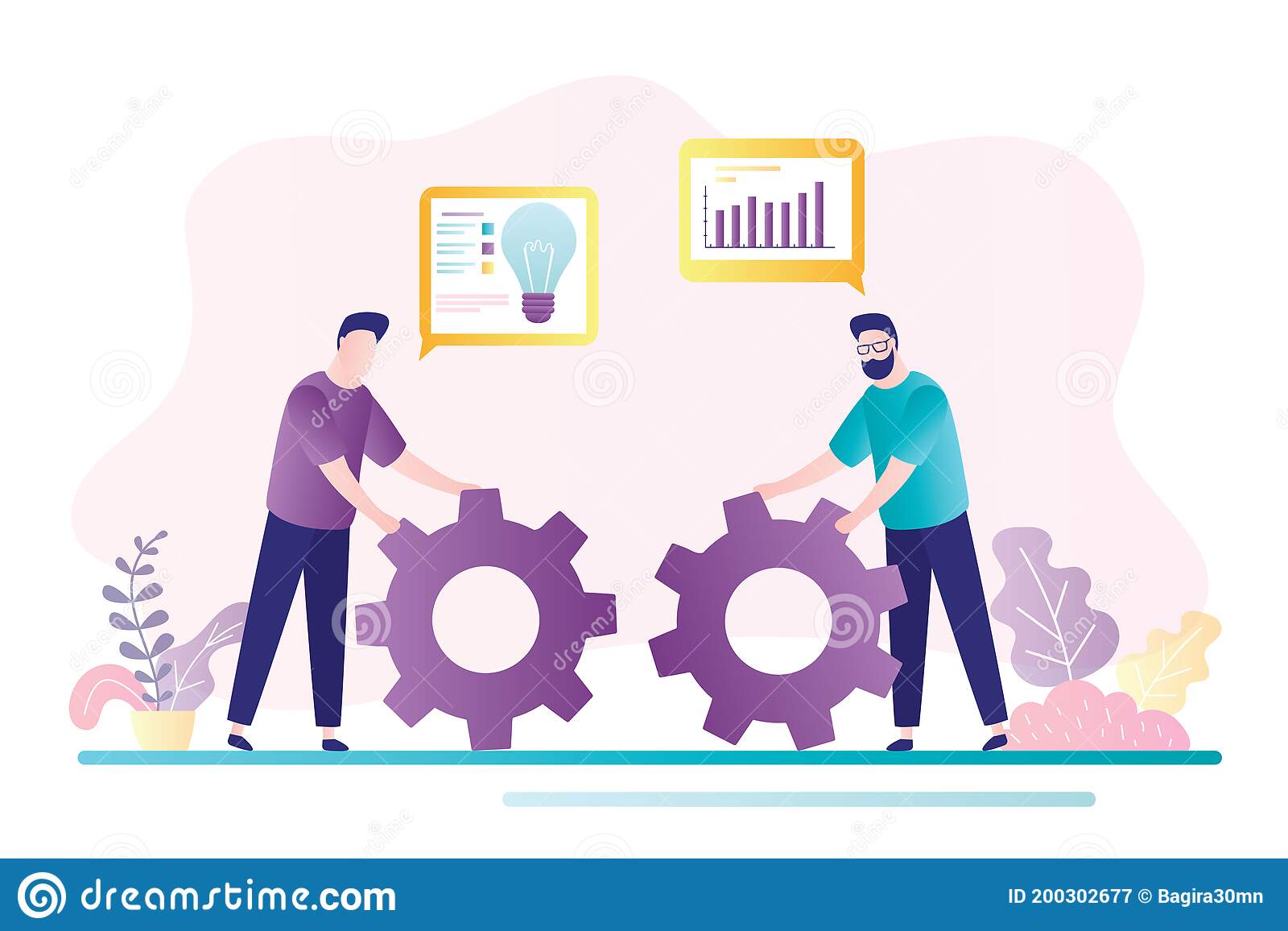
Creating a positive working environment is a crucial step in ensuring the wellbeing of your employees. This will increase productivity, reduce burnout, and decrease complaints. Several studies have shown that employees who are happy and motivated work more effectively. Before creating a positive environment for your employees, there are several things you need to consider.
Positive work environment encourages productivity
Positive working environments create a calm environment that encourages employees to be more productive and stay focused. It fosters cognitive and physical well-being. Clear communication is a hallmark of a positive working environment. This kind of work environment provides employees with the chance to ask questions, and receive constructive feedback.
A positive work environment encourages employees 200% effort. They do not hesitate to take responsibility for their actions and will not play revenge if they receive negative feedback. It fosters friendship, camaraderie, and healthy competition. It encourages employees to take time off and enjoy what they do.
Employees are happier
An environment that is positive and supportive of your employees will make them happy. Employees who are happy at their job are more productive and are more likely sharing their ideas with others. They also feel less stressed and more satisfied, and are less likely to take sick days.
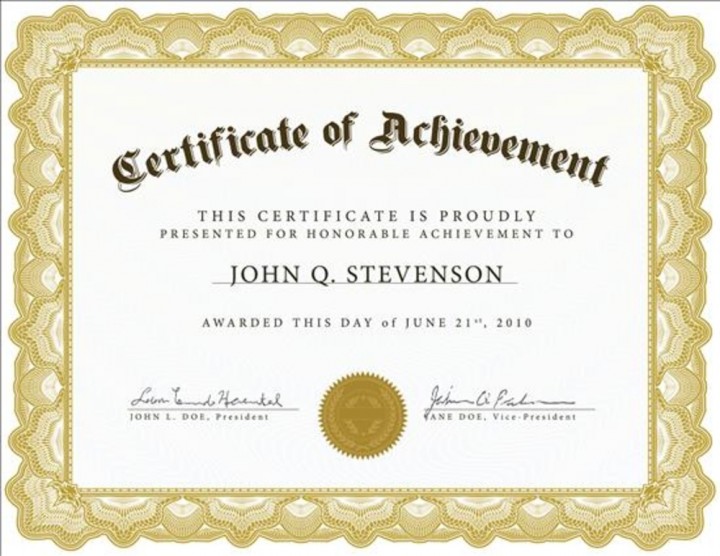
University of Birmingham research suggests that positive work environments can result in greater employee happiness. When employees are happy, they work more efficiently, make more call-to-sale conversions per hour, and adhere to their workflow schedule.
It is possible to reduce burnout
Burnout can cause serious damage to productivity and health. It is essential that organizations have a plan in place to prevent this. Burnout is a psychosocial condition that impacts working relationships. It is characterized by a lack of empathy and emotional detachment from patients and colleagues. Research has shown this condition can be prevented by proactive actions such as creating positive working environments.
Positive work environments can help reduce burnout by increasing individual and team efficacy. Empowerment increases individual efficacy which can help to mitigate the effects of exhaustion and cynicism. Staff communication improves team efficacy and is directly linked to personal efficacy.
It reduces complaints
Positive working environments make employees feel happy about their jobs. A positive work environment is more conducive to employees staying focused on their tasks and completing them on time. They are also more productive and have a higher employee status. Positive work environments encourage collaboration. Employees can express themselves and get feedback to improve performance.
Businesses can reduce complaints by creating a positive work environment. The first step is to create an environment that is free of harassment, bullying, and discrimination. A great place to work is one that is free from harassment, bullying, and discrimination. Positive working environments improve employee morale and reduce complaints, as well as employee stress.
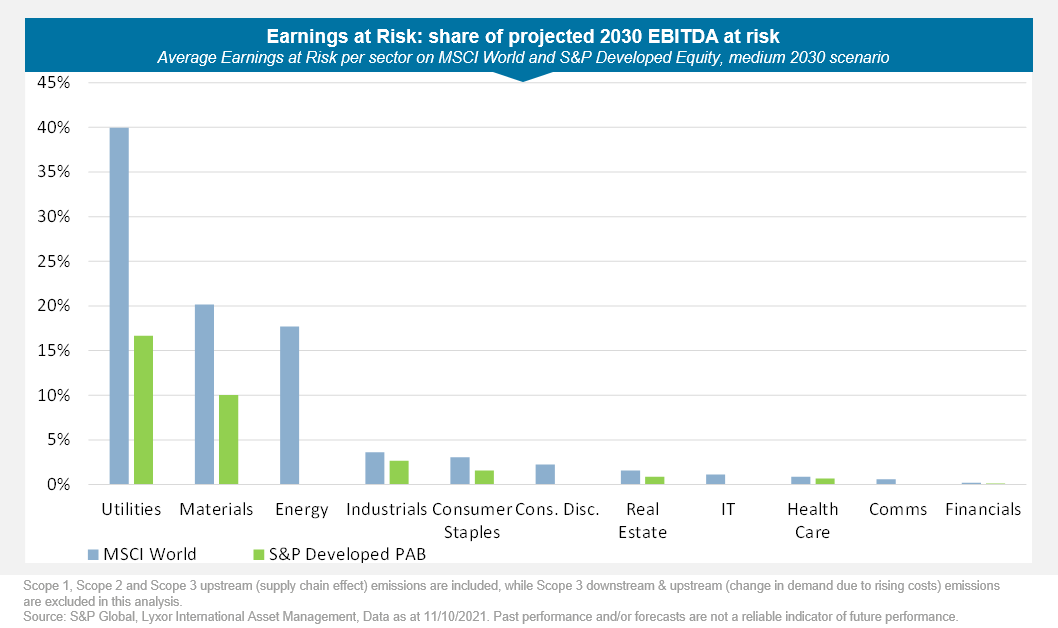
It improves teacher wellbeing
Teacher wellbeing can be affected by the quality of their work environment. There are many ways to improve teacher wellness, including providing a supportive environment for staff and hosting regular meetings. An audit of the wellbeing of teachers in schools can provide an indication of their current state and help them to set goals for improvement.
Teachers are exposed to a thousand different interactions every day, and the quality of those interactions is critical to their well-being. Studies have shown that a toxic culture can lead to poor teacher wellbeing. A supportive environment will support healthy practices and enable teachers to focus on their students. Teachers also require ongoing professional development. A survey found that teachers want PD for teacher well-being to be widely available and standard practice.
FAQ
What is the main difference between Six Sigma Six Sigma TQM and Six Sigma Six Sigma?
The main difference between these two quality management tools is that six sigma focuses on eliminating defects while total quality management (TQM) focuses on improving processes and reducing costs.
Six Sigma can be described as a strategy for continuous improvement. It emphasizes the elimination or minimization of defects through statistical methods such control charts and p charts.
This method seeks to decrease variation in product output. This is done by identifying and correcting the root causes of problems.
Total quality management refers to the monitoring and measurement of all aspects in an organization. It also includes training employees to improve performance.
It is used to increase productivity.
What is TQM?
The quality movement was born during the industrial revolution when manufacturing companies realized they could not compete on price alone. If they wanted to stay competitive, they needed to improve their quality and efficiency.
Management realized the need to improve and created Total Quality Management, which focused on improving all aspects within an organization's performance. It involved continuous improvement, employee participation, and customer satisfaction.
Which kind of people use Six Sigma
Six sigma is a common concept for people who have worked in statistics or operations research. Anyone involved in business can benefit.
It requires high levels of commitment and leadership skills to be successful.
What are the steps to take in order to make a management decision?
Managers face complex and multifaceted decision-making challenges. It includes many factors such as analysis, strategy planning, implementation and measurement. Evaluation, feedback and feedback are just some of the other factors.
Remember that people are humans just like you, and will make mistakes. This is the key to managing them. You are always capable of improving yourself, and there's always room for improvement.
We explain in this video how the Management decision-making process works. We discuss the different types of decisions and why they are important, every manager should know how to navigate them. The following topics will be covered:
What are the five management processes?
Each business has five stages: planning, execution and monitoring.
Planning involves setting goals for the future. Planning includes setting goals for the future.
Execution occurs when you actually carry out the plans. It is important to ensure that everyone follows the plans.
Monitoring allows you to monitor your progress towards achieving your goals. Regular reviews of performance against targets, budgets, and other goals should be part.
Review events take place at each year's end. They provide an opportunity to assess whether everything went well during the year. If not then, you can make changes to improve your performance next year.
After the annual review, evaluation takes place. It helps identify which aspects worked well and which didn't. It also provides feedback on the performance of people.
Statistics
- Our program is 100% engineered for your success. (online.uc.edu)
- The BLS says that financial services jobs like banking are expected to grow 4% by 2030, about as fast as the national average. (wgu.edu)
- The profession is expected to grow 7% by 2028, a bit faster than the national average. (wgu.edu)
- As of 2020, personal bankers or tellers make an average of $32,620 per year, according to the BLS. (wgu.edu)
- This field is expected to grow about 7% by 2028, a bit faster than the national average for job growth. (wgu.edu)
External Links
How To
How can you implement the Kaizen technique?
Kaizen means continuous improvement. The term was coined in the 1950s at Toyota Motor Corporation and refers to the Japanese philosophy emphasizing constant improvement through small incremental changes. It's a team effort to continuously improve processes.
Kaizen, a Lean Manufacturing method, is one of its most powerful. This concept requires employees to identify and solve problems during manufacturing before they become major issues. This will increase the quality and decrease the cost of the products.
Kaizen is about making everyone aware of the world around them. Correct any errors immediately to avoid future problems. If someone is aware of a problem at work, he/she should inform his/her manager immediately.
Kaizen is based on a few principles. Always start with the end product in mind and work our way back to the beginning. We can improve the factory by first fixing the machines that make it. Next, we repair the machines that make components. Then, the machines that make raw materials. Then we fix the workers, who directly work with these machines.
This approach is called 'kaizen' because it focuses on improving everything steps by step. When we are done fixing the whole factory, we go back to the beginning and continue until we reach perfection.
How to measure kaizen's effectiveness in your business is essential to implement it. There are many ways to tell if kaizen is effective. Another method is to see how many defects are found on the products. Another way is to see how much productivity has increased since implementing kaizen.
Another way to know whether kaizen is working is to ask yourself why did you decide to implement kaizen. Did you do it because it was legal or to save money? Did you really think that it would help you achieve success?
Congratulations if you answered "yes" to any of the questions. You're ready to start kaizen.