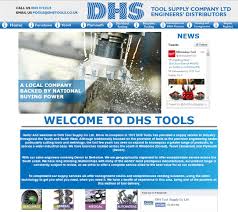
Ad-hoc jobs are a term to describe a temporary job. This type of project requires the right people who have specific skills that relate to the project and have the time to dedicate to it. Project managers will often consult with others in departments to determine the necessary number of people to complete the task. They will then need to send requests to those people who are qualified for the project.
Manage ad hoc Projects
If you work in a job where you get ad hoc projects on a regular basis, you should establish a process to manage them. You can do this by keeping a project log that includes information about due dates and tasks. This will allow you to recall the tasks and keep track of other people's progress, which will improve communication and management. You should also update your log when tasks change or new tasks arise.
Ad hoc projects require that everyone be on the same page regarding what is expected. This is especially important for projects that involve collaboration among multiple stakeholders. It's not possible to wait for the information to flow down through bureaucracy. All members of the team need to know the scope and goals of the project. If someone isn’t sure of the project’s goals, they can seek out the assistance of someone who does.
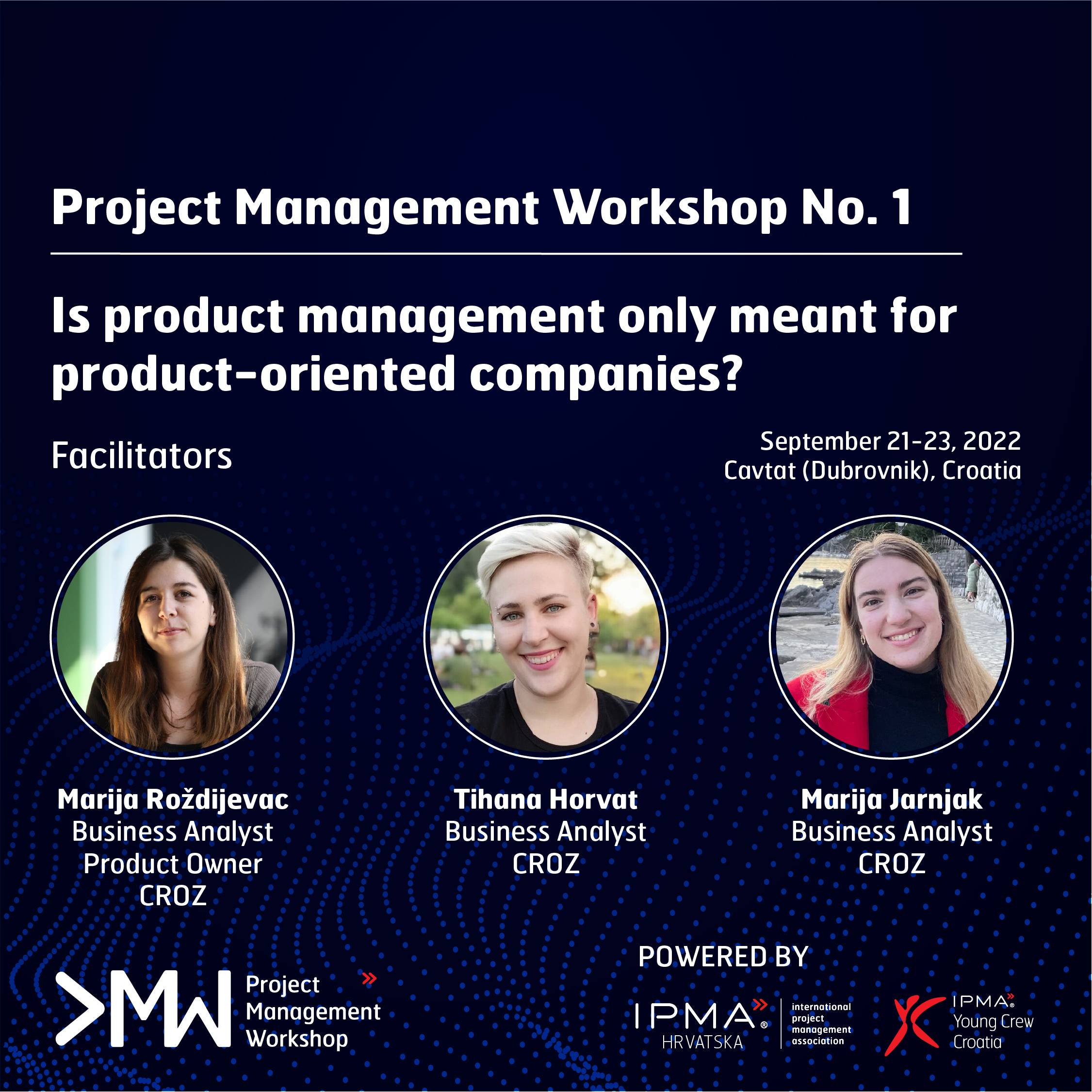
Ad-hoc projects are usually temporary and do not require long-term commitments. They are often short-term, require multiple items and rely on multiple people. The project manager will need to coordinate a team and allocate resources accordingly.
Manage ad hoc workers
An ad-hoc job may require you to manage several people, some of whom may not be on your regular payroll. You must ensure they have the required skills and are available to work on the project. In such situations, you may need to consult other department managers for help. Determine how many people are needed and then send requests for resources.
A good system can make managing ad-hoc projects easier. This will allow you to see the resources available and how they are being used. This will allow you to make better decisions regarding the management of the project. It's crucial to keep track if you work with an ad hoc group.
You can choose to have ad-hoc work done by employees or contractors. These projects can be part-time or full-time and are great for projects that don’t interrupt ongoing initiatives. But, being unprepared for the unexpected can lead to inefficiencies, waste of resources, and even miss your project goals.
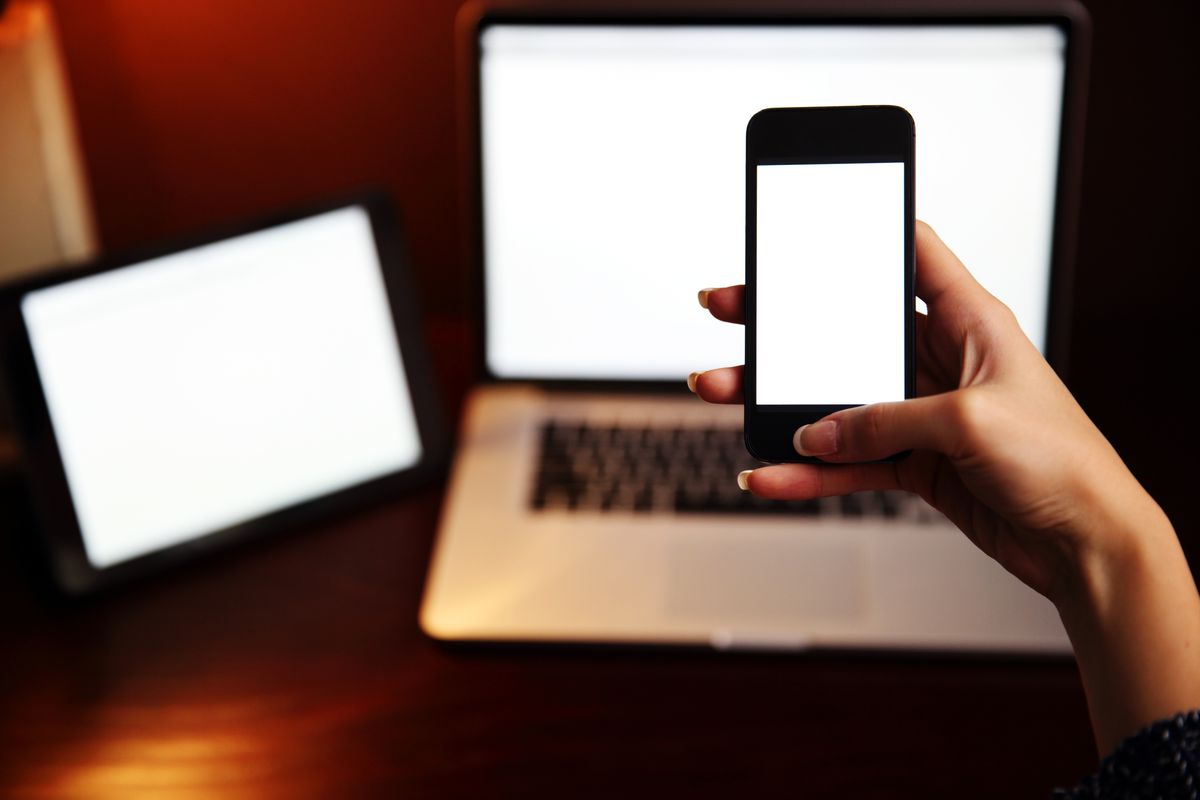
Although ad hoc requests may be convenient, they can also cause problems for your entire team. Your marketing team should prioritize the requests and determine what is more important. You need to be able to manage ad hoc requests before they become a problem for your team's productivity.
FAQ
What are some common mistakes managers make?
Sometimes managers make it harder for their employees than is necessary.
They may not delegate enough responsibilities to staff and fail to give them adequate support.
Many managers lack the communication skills to motivate and lead their employees.
Managers set unrealistic expectations and make it difficult for their team.
Managers may prefer to solve every problem for themselves than to delegate responsibility.
Why does it sometimes seem so difficult to make good business decisions?
Complex systems and many moving parts make up businesses. The people who run them must juggle multiple priorities at once while also dealing with uncertainty and complexity.
Understanding how these factors impact the whole system is key to making informed decisions.
You need to be clear about the roles and responsibilities of each system. Next, consider how each piece interacts with the others.
Also, you should ask yourself if there have been any assumptions in your past behavior. If you don't have any, it may be time to revisit them.
You can always ask someone for help if you still have questions after all of this. They might see things differently than you and may have some insights that could help find a solution.
What is Kaizen?
Kaizen refers to a Japanese term that stands for "continuous improvements." It is a philosophy which encourages employees in continuously improving their work environment.
Kaizen is founded on the belief of everyone being able to do their job well.
How can we create a successful company culture?
A successful company culture is one that makes people feel valued and respected.
It is founded on three basic principles:
-
Everyone has something valuable to contribute
-
People are treated fairly
-
There is mutual respect between individuals and groups
These values are reflected in the way people behave. They will treat others with consideration and courtesy.
They will respect other people's opinions.
They can also be a source of inspiration for others.
Company culture also encourages open communication, collaboration, and cooperation.
People are free to speak out without fear of reprisal.
They are aware that mistakes can be accepted if they are treated honestly.
Finally, the company culture promotes integrity and honesty.
Everyone understands that the truth is always best.
Everyone is aware that rules and regulations apply to them.
And no one expects special treatment or favors.
What is Six Sigma?
It's a strategy for quality improvement that emphasizes customer care and continuous learning. The objective is to eliminate all defects through statistical methods.
Motorola's 1986 efforts to improve manufacturing process efficiency led to the creation of Six Sigma.
It was quickly adopted by the industry and many companies are now using six-sigma to improve product design, production, delivery, customer service, and product design.
How does Six Sigma work?
Six Sigma employs statistical analysis to identify problems, measure them and analyze root causes. Six Sigma also uses experience to correct problems.
The first step in solving a problem is to identify it.
Next, data is collected and analyzed to identify trends and patterns.
Then, corrective actions can be taken to resolve the problem.
Final analysis of data is done to determine if the problem has been solved.
This continues until the problem has been solved.
Statistics
- The profession is expected to grow 7% by 2028, a bit faster than the national average. (wgu.edu)
- As of 2020, personal bankers or tellers make an average of $32,620 per year, according to the BLS. (wgu.edu)
- The BLS says that financial services jobs like banking are expected to grow 4% by 2030, about as fast as the national average. (wgu.edu)
- This field is expected to grow about 7% by 2028, a bit faster than the national average for job growth. (wgu.edu)
- Your choice in Step 5 may very likely be the same or similar to the alternative you placed at the top of your list at the end of Step 4. (umassd.edu)
External Links
How To
What is Lean Manufacturing?
Lean Manufacturing processes are used to reduce waste and improve efficiency through structured methods. These processes were created by Toyota Motor Corporation, Japan in the 1980s. The main goal was to produce products at lower costs while maintaining quality. Lean manufacturing eliminates unnecessary steps and activities from a production process. It has five components: continuous improvement and pull systems; just-in time; continuous change; and kaizen (continuous innovation). Pull systems are able to produce exactly what the customer requires without extra work. Continuous improvement is constantly improving upon existing processes. Just-in-time refers to when components and materials are delivered directly to the point where they are needed. Kaizen means continuous improvement. Kaizen involves making small changes and improving continuously. Fifth, the 5S stand for sort, set up in order to shine, standardize, maintain, and standardize. These five elements work together to produce the best results.
Lean Production System
Six key concepts form the foundation of the lean production system:
-
Flow - focuses on moving information and materials as close to customers as possible.
-
Value stream mapping: This is a way to break down each stage into separate tasks and create a flowchart for the entire process.
-
Five S's, Sort, Set in Order, Shine. Standardize. and Sustain.
-
Kanban - visual cues such as stickers or colored tape can be used to track inventory.
-
Theory of constraints: identify bottlenecks in your process and eliminate them using lean tools, such as kanban board.
-
Just-intime - Order components and materials at your location right on the spot.
-
Continuous improvement: Make incremental improvements to the process instead of overhauling it completely.