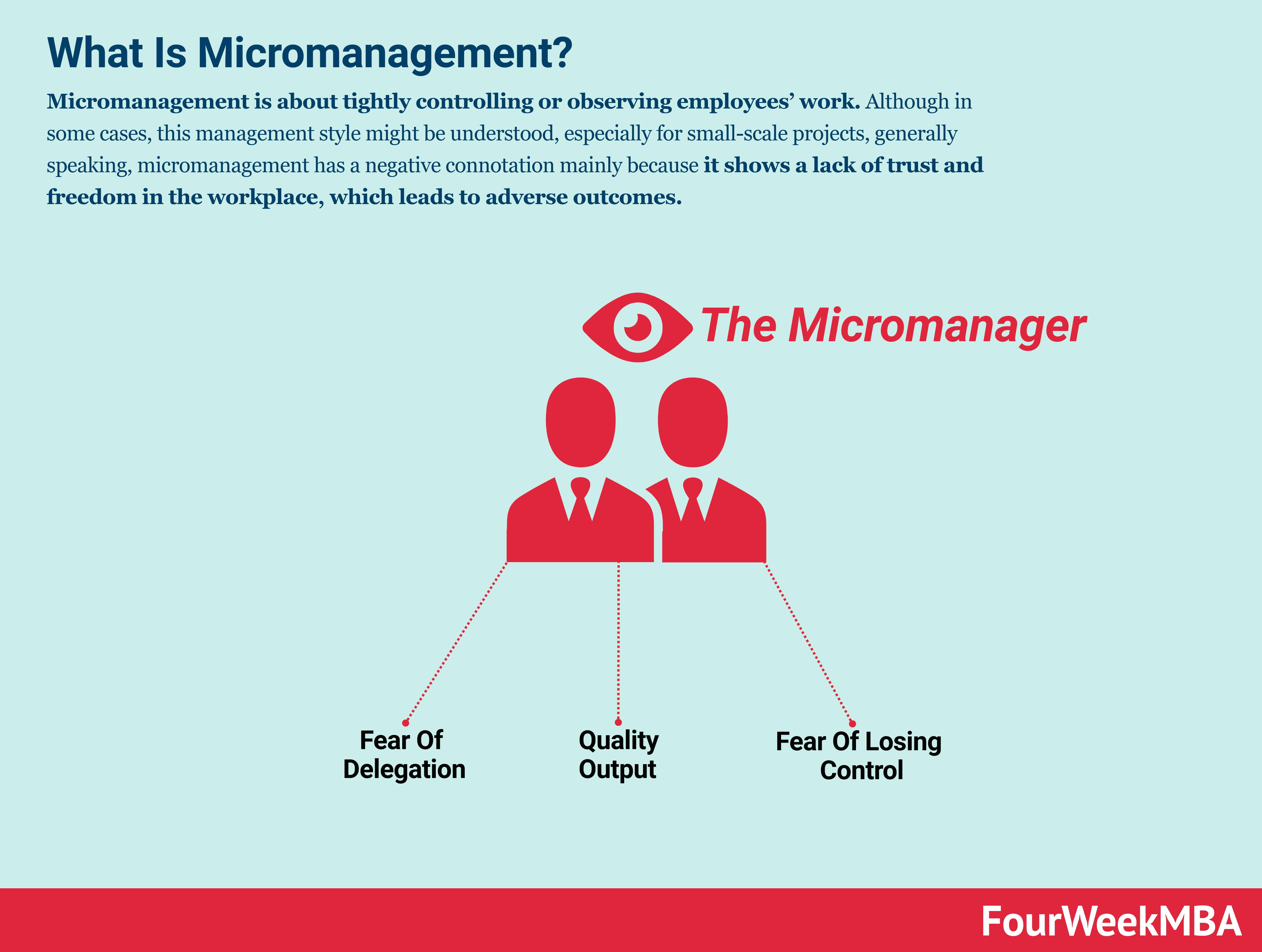
You can use a continuous improvement method to get the desired results over time. This method involves iterative design processes over multiple generations. It is also known under the name Lean Six Sigma. This article will discuss one variation of the PDSA technique based on SIPOC analysis. Its application is discussed within an engineering design workshop.
Lean Six Sigma
Lean Six Sigma, a method for continuous improvement, focuses on making processes more predictable and simpler. The risk of process errors being overlooked is reduced when processes are simplified. The method uses statistical process control methods (SPC) to improve process performance and control variables. It can be used to improve any process, product, or service. The company must establish clear measurable characteristics and use data to guide the changes.
PDSA
The PDSA continuous improvement method uses a continuous loop that includes process design, analysis, action, and monitoring to improve a company's business processes. The initial phase of PDSA, known as the study step, evaluates the results of an experimental improvement in comparison to the planned results. This step allows the team to determine if the improvement was a success. The team will often conduct analysis and use control charts to determine if there is any special cause variation.
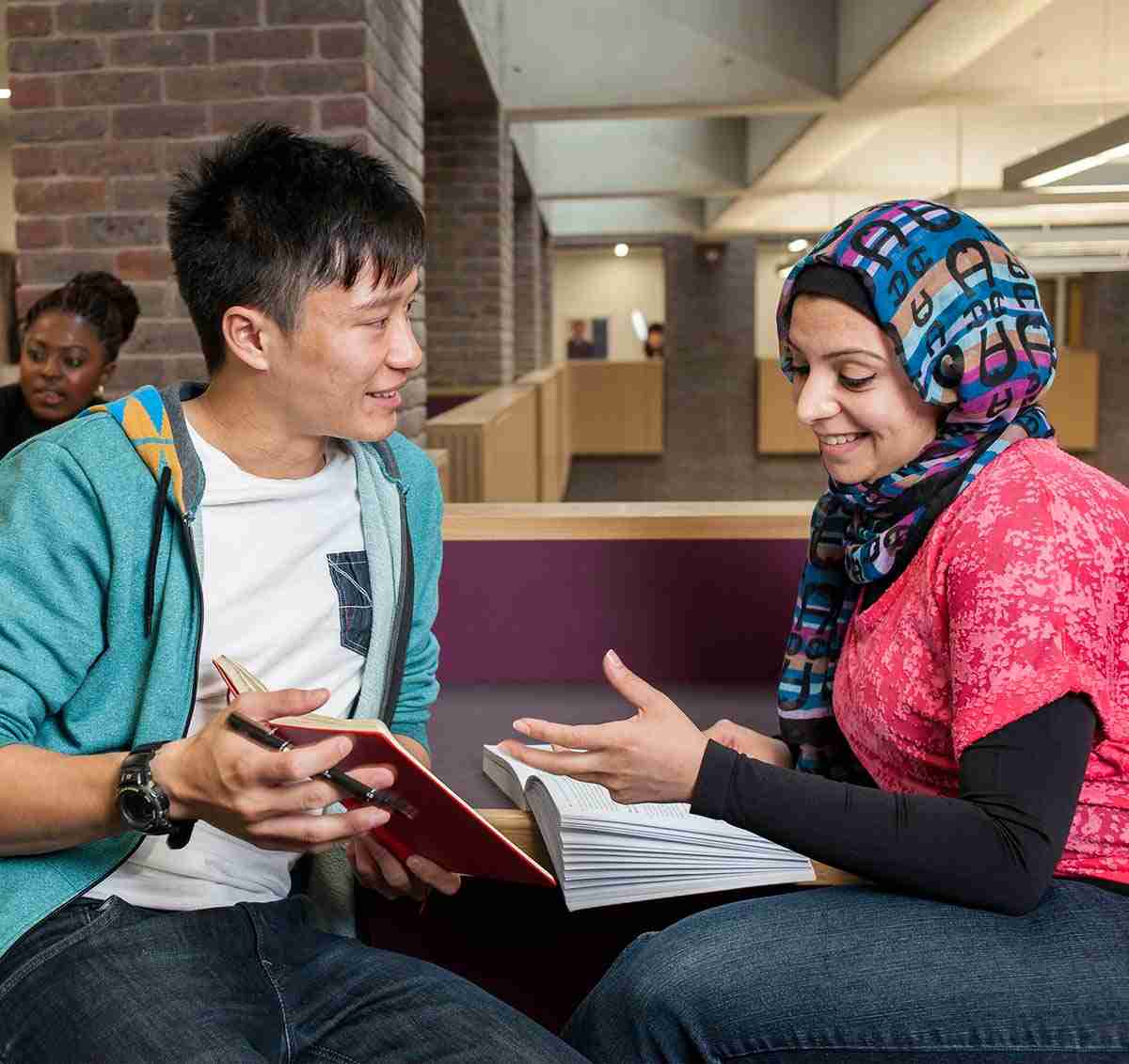
Variation of PDSA
PDSA (Personal Development and Support) is a method of continuous improvement and problem-solving, with a clearly defined focus and measurable targets. It begins with careful planning, then moves to the actual action stage. Every idea is then tested and evaluated for its feasibility and sustainability. The project team measures the results to ensure that any changes will result in lasting improvements.
PDSA based upon SIPOC analysis
SIPOC analysis is a useful tool for improving business processes. It is an easy-to-use method of categorizing data under 5 categories. SIPOC diagrams help teams understand their processes better by giving a high level overview of each. These diagrams are also great for focusing discussions.
PDSA based upon DMAIC
Continuous improvement methodologies that follow the DMAIC process are useful for organizations seeking to improve their processes. These methods are easy to follow and are structured so that organizations can understand and eliminate inefficient processes. Additionally, they help them achieve measurable results. Without the use of these tools, organizations may struggle to track which changes have the greatest impact and which ones don't. They can also have a difficult time implementing effective controls.
PDSA based off kanban boards
Kanban boards offer many benefits. Kanban boards allow you to visualize your work, assign tasks to other team members, and include attachments, images, or videos for each task. You can also control how much work is done and when it is finished.

Kaizen is based on SIPOC analysis
The SIPOC model can be used as a powerful framework and concept in process improvement efforts. It is useful in helping to establish the boundaries of a process, collect relevant information, and make it clear and easy to understand. It is useful in the Define phase, which is part of DMAIC methodologies, to identify process variations and key performance indicator (KVIPs) that can affect KVIPs. It aids teams and stakeholders in planning improvements to improve processes.
PDSA based PDSA variation
Continuous improvement methodology PDSA uses the principle of continuous comparison between actual and expected results. The PDSA methodology measures the actual results of an improvement project against the expected outcomes. Then the reality of implementation is compared with that plan. The team then analyzes the data to determine whether the experiment produced measurable improvements. The team often uses a control chart to distinguish between expected variation or special cause variation.
FAQ
What is the difference between Six Sigma Six Sigma and TQM?
The main difference in these two quality management tools lies in the fact that six sigma is focused on eliminating defects and total quality management (TQM), emphasizes improving processes and reducing costs.
Six Sigma is a methodology for continuous improvement. It emphasizes the elimination or minimization of defects through statistical methods such control charts and p charts.
This method attempts to reduce variations in product output. This is done by identifying and correcting the root causes of problems.
Total quality management is the measurement and monitoring of all aspects within an organization. This includes training employees to improve their performance.
It is often used to increase productivity.
What are management theories?
Management concepts are the practices and principles managers use to manage people or resources. These include topics such as human resource policies and job descriptions, performance assessments, training programs and employee motivation.
What are some of the common mistakes made by managers?
Managers sometimes make their own job harder than necessary.
They might not give enough support and delegate the right responsibilities to their staff.
A majority of managers lack the communication skills needed to motivate their team and lead them.
Managers can set unrealistic expectations for their employees.
Managers might try to solve every problem by themselves rather than delegating the responsibility.
What is the difference between leadership and management?
Leadership is about being a leader. Management is about controlling others.
A leader inspires others while a manager directs them.
Leaders motivate people to succeed; managers keep workers on track.
A leader develops people; a manager manages people.
Statistics
- The BLS says that financial services jobs like banking are expected to grow 4% by 2030, about as fast as the national average. (wgu.edu)
- UpCounsel accepts only the top 5 percent of lawyers on its site. (upcounsel.com)
- Your choice in Step 5 may very likely be the same or similar to the alternative you placed at the top of your list at the end of Step 4. (umassd.edu)
- Hire the top business lawyers and save up to 60% on legal fees (upcounsel.com)
- As of 2020, personal bankers or tellers make an average of $32,620 per year, according to the BLS. (wgu.edu)
External Links
How To
How do I get my Six Sigma license?
Six Sigma is a quality control tool that improves processes and increases efficiency. It is a process that helps businesses achieve consistent results in their operations. The name derives its meaning from the "sigmas" Greek word, which is composed of two letters that mean six. Motorola was the first to develop this process. Motorola realized they needed to standardize the manufacturing processes to produce products faster and cheaper. There were many people doing the work and they had difficulty achieving consistency. To resolve this issue, they used statistical tools like Pareto analysis and control charts. These techniques would be applied to every aspect of the operation. This technique would enable them to make improvements in areas that needed it. The Six Sigma certification process involves three major steps. Find out if you are qualified. Before you take any exams, you'll need to take some classes. Once you've passed those classes, you'll start taking the tests. You will want to remember everything you learned in the class. Once you have completed the class, you will be ready for the test. You will be certified if you pass the test. Final, your certifications can be added to you resume.