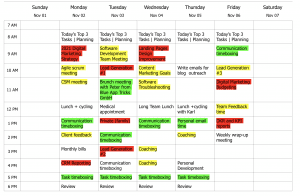
To be considered a PSM program, a company must comply with 14 elements. These elements include process hazard analyses and permissible exposure limits. These elements are essential for the success of a PSM plan. Compliant PSM programs will be judged compliant if they adhere to these elements. These elements and their application to your company are covered in the sections below.
Analyses of process hazards
A process hazards analysis is an important component of safety management programs. It helps to identify potential hazards as well as evaluate the consequences. This analysis must be done by a team of employees who are knowledgeable about the process. It will also include information about human factors and past incidents. Once the analysis is complete, it must be updated at least every five years. The safety management system must include hazard analysis.
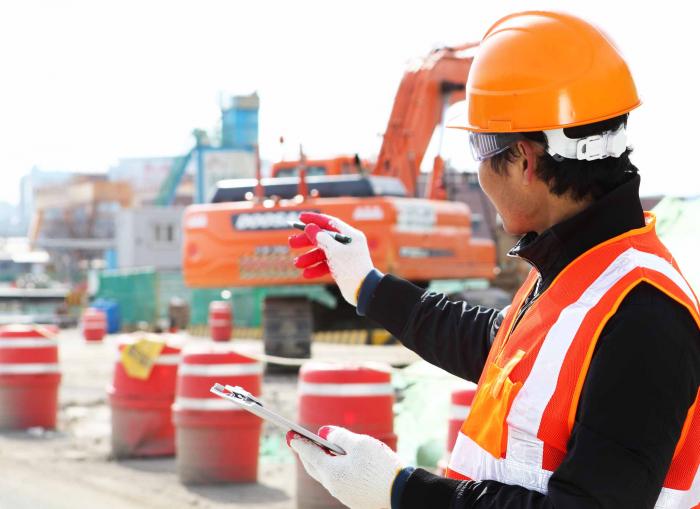
Permissible exposure limits
OSHA Process Safety Management Standard is a set standards that govern processes that involve hazardous chemicals, gases, or fluids. The standard applies to all businesses that produce or process hazardous chemical products. It does not cover hydrocarbon fuels used exclusively for workplace use, retail or well drilling. It does not apply to facilities that are normally vacant or remote.
Physical data
PSM is the process for analyzing and controlling hazardous materials and products. This is the process of safely handling, transporting, and storing hazardous substances. This can lead to less product waste and fewer workplace accidents. It makes it easier to make decisions and allows organizations to prioritize safety and health. PSM is essential for a safe workplace. It can help companies prevent costly medical emergencies and save money.
Corrosivity data
The PSM standard describes requirements for chemical storage and handling. The PSM requires periodic compliance audits and includes requirements for emergency plans and permit system. A workplace that is compliant with the PSM will be safe and protect employees from harm and accidents, regardless of whether hazardous substances are used in production.
Thermal stability data
OSHA established a standard to collect and report PSM thermal stability data. This program will make sure researchers are well-informed about possible hazards and minimize accidental releases. It will be updated regularly to reflect new research tasks. It will be accessible to all employees. The PSM program includes information on toxicity, reactivity, corrosivity, and physical properties.

Employee participation clause
Process Safety Management (PSM), is a systematic and analytical approach to preventing process accidents due to highly hazardous chemicals (HHC). It is an important step in improving process safety and must be implemented at all levels, including maintenance and production. It contains 14 elements and employee participation clauses that must all be implemented. These elements and their requirements are listed below.
FAQ
What's the difference between Six Sigma and TQM?
The major difference between the two tools for quality management is that six Sigma focuses on eliminating defect while total quality control (TQM), on improving processes and decreasing costs.
Six Sigma can be described as a strategy for continuous improvement. It emphasizes the elimination of defects by using statistical methods such as control charts, p-charts, and Pareto analysis.
This method seeks to decrease variation in product output. This is done by identifying root causes and rectifying them.
Total Quality Management involves monitoring and measuring every aspect of the organization. It also includes training employees to improve performance.
It is used to increase productivity.
What are the top management skills?
Any business owner needs to be able to manage people, finances, resources and time. They are the ability to manage people and finances, space, money, and other factors.
When you need to manage people, set goals, lead teams, motivate them, solve problems, develop policies and procedures and manage change, management skills are essential.
As you can see, there are many managerial responsibilities!
What do we mean when we say "project management"?
It refers to the management of activities related to a project.
Our services include the definition of the scope, identifying requirements, preparing a budget, organizing project teams, scheduling work, monitoring progress and evaluating the results before closing the project.
Statistics
- Our program is 100% engineered for your success. (online.uc.edu)
- UpCounsel accepts only the top 5 percent of lawyers on its site. (upcounsel.com)
- This field is expected to grow about 7% by 2028, a bit faster than the national average for job growth. (wgu.edu)
- As of 2020, personal bankers or tellers make an average of $32,620 per year, according to the BLS. (wgu.edu)
- The BLS says that financial services jobs like banking are expected to grow 4% by 2030, about as fast as the national average. (wgu.edu)
External Links
How To
How can you apply the 5S in the office?
To make your workplace more efficient, organize everything. A clean desk, a tidy room, and a well-organized workspace help everyone stay productive. The five "S"'s (Sort. Shine. Clean. Separate. And Store) help to maximize space and ensure efficiency. In this session, we'll go through these steps one at a time and see how they can be implemented in any type of environment.
-
Sort. Get rid of clutter and papers so you don't have to waste time looking for the right item. This means you place items where you will use them the most. If you frequently refer back to something, put it near the place where you look up information or do research. It is important to consider whether or not you actually need something. If it does not serve a purpose, get rid of it.
-
Shine. Don't leave anything that could damage or cause harm to others. Find a safe way to store pens that you don't want anyone else to see. A pen holder might be a good investment, as it will prevent you from losing pens.
-
Sweep. To prevent dirt buildup on furniture and other items, clean them regularly. To keep surfaces as clean as you can, invest in dusting equipment. You can also set aside an area to sweep and dust in order to keep your workstation clean.
-
Separate. Separate your trash into multiple bins to save time when you have to dispose of it. You can dispose of your garbage easily by placing trash cans strategically around the office. Make sure that you take advantage of this location by placing trash bags next to each bin so that you don't have to dig through piles of trash to find what you need.