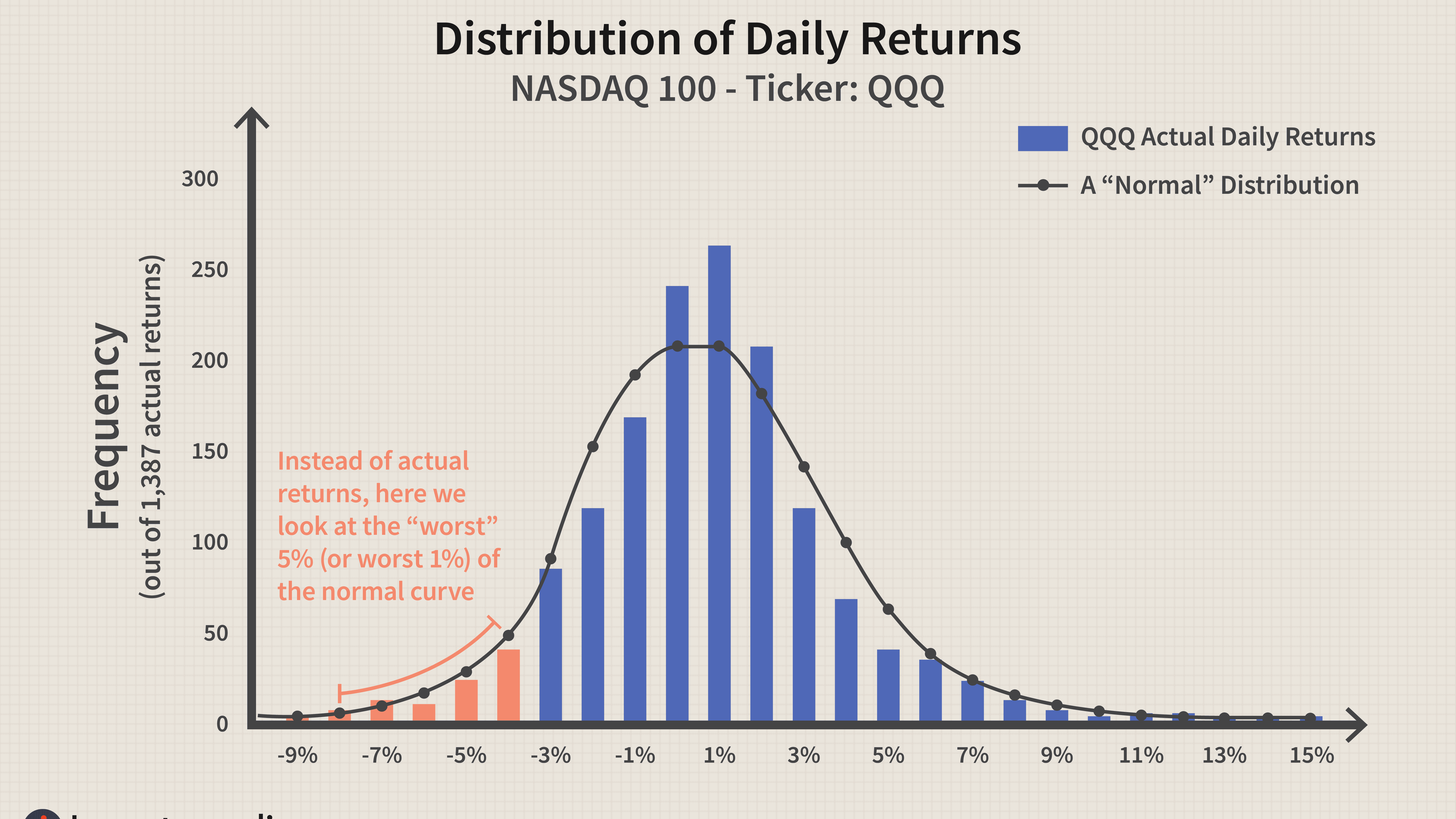
If you are having trouble logging into the Waste Management website, you may have two main reasons. You might need to wait a while for the server to get back online. You may have entered incorrect login credentials. Check your data connection to see if you have problems. Check the status of your third-party social media network to see if it is working. You can also read the error messages sent to you by third-party social networks to learn why you aren't able log in.
Sign in to Gilton Solid Waste Management
Gilton Solid Waste Management can be signed in by business owners or managers who use an online bill pay service. You have the option of paying by credit card, direct payment, or bank account. These methods of payment are convenient and stress-free, and you can set them up to automatically pay your bill each month. For added security, doxo shows fees and other relevant information before you proceed.
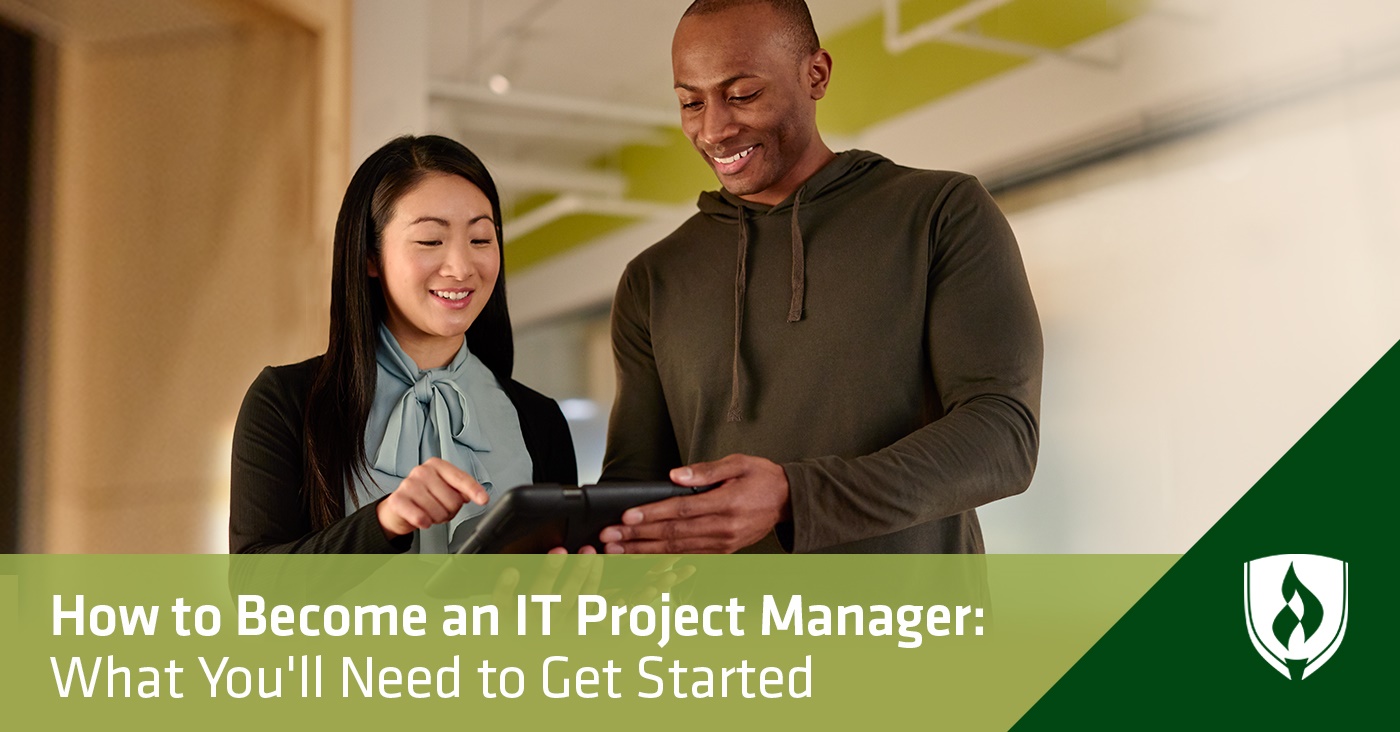
Gilton Solid Waste Management specializes as a full service waste management company. Gilton Solid Waste Management can pick up your garbage if it is located in Waterford. Signing up for a service requires proof of residency and age. To have your trash picked out, you will also need to schedule an appointment. There are only two (2) times you can schedule garbage pickup. Gilton Solid Waste Management also takes Christmas trees. You can place your tree in front your home to make sure it gets picked up.
Signing up to MyWMTotalRewards
Enter your email address and password to sign in at MyWMTotalRewards. If you have a customer identification, you will also need it. You will also need to enter your billing zip code. Once you've entered all the information, you are good to go. After creating your account, you can customize the features available to you. You can create your own schedule, schedule regular waste pickups, receive holiday closure notifications, and even create your own schedule.
Signing up for MyWMTotalRe rewards in waste management is simple. To sign in to MyWMTotalRe rewards for waste management in Canada, your employee ID can be used. The customer ID is the number on your invoice. It's usually located in the upper right corner. This number can be used for many purposes, such as logging in to your account or setting up online transactions.
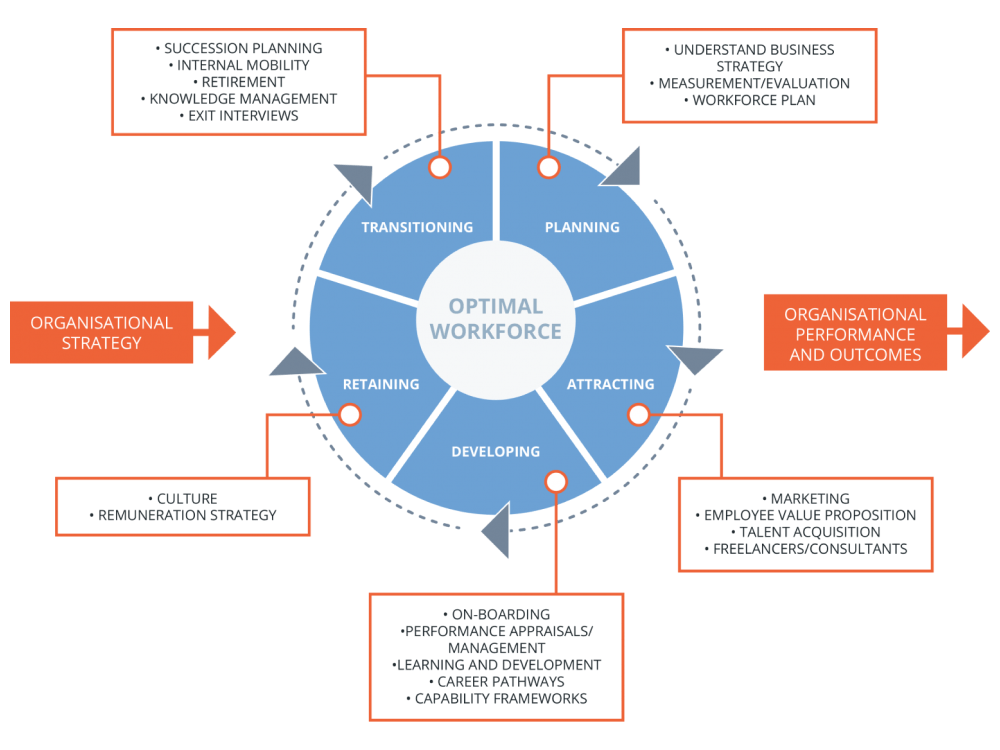
Recovering your login password
If you can't remember your Waste Management login password, you can reset it. To do this, simply type your email address in the field provided. In a matter of minutes, a new password will be sent and you can then log back in with it. You can also use your mobile phone number, email or phone number to determine your password. To reset the password, click on "Send".
FAQ
How to effectively manage employees
Managing employees effectively means ensuring that they are happy and productive.
It also means having clear expectations of their behavior and keeping track of their performance.
Managers must set clear goals for their employees and themselves to achieve this goal.
They should communicate clearly with employees. And they need to ensure that they reward good performance and discipline poor performers.
They will also need to keep records about their team's activities. These include:
-
What did you accomplish?
-
What was the work involved?
-
Who did it, anyway?
-
When it was done?
-
Why was this done?
This information can be used to monitor performance and evaluate results.
What is Six Sigma and how can it help you?
It is a way to improve quality that places emphasis on customer service and continuous learning. The goal is to eradicate defects through statistical techniques.
Motorola created Six Sigma as part of their efforts to improve manufacturing processes in 1986.
It was quickly adopted by the industry and many companies are now using six-sigma to improve product design, production, delivery, customer service, and product design.
What is the difference between Six Sigma Six Sigma and TQM?
The main difference between these two quality-management tools is that six-sigma concentrates on eliminating defects while total QM (TQM), focuses upon improving processes and reducing expenses.
Six Sigma can be described as a strategy for continuous improvement. It emphasizes the elimination of defects by using statistical methods such as control charts, p-charts, and Pareto analysis.
This method aims to reduce variation in product production. This is accomplished by identifying the root cause of problems and fixing them.
Total quality management includes monitoring and measuring all aspects of an organization's performance. Training employees is also part of total quality management.
It is used to increase productivity.
What are the 3 main management styles?
There are three main management styles: participative, laissez-faire and authoritarian. Each style has its advantages and disadvantages. Which style do yo prefer? Why?
Autoritarian - The leader sets direction and expects everyone else to follow it. This style works well if an organization is large and stable.
Laissez-faire – The leader gives each individual the freedom to make decisions for themselves. This style works best when the organization is small and dynamic.
Participative - Leaders listen to all ideas and suggestions. This style is best for small organizations where everyone feels valued.
What is Kaizen?
Kaizen is a Japanese term meaning "continuous improvement." It is a philosophy that encourages employees to constantly look for ways to improve their work environment.
Kaizen is founded on the belief of everyone being able to do their job well.
What is TQM exactly?
The industrial revolution led to the birth and growth of the quality movement. Manufacturing companies realized they couldn't compete solely on price. They needed to improve the quality and efficiency of their products if they were to be competitive.
In response to this need for improvement, management developed Total Quality Management (TQM), which focused on improving all aspects of an organization's performance. It included continuous improvement, employee involvement and customer satisfaction.
Statistics
- Your choice in Step 5 may very likely be the same or similar to the alternative you placed at the top of your list at the end of Step 4. (umassd.edu)
- Our program is 100% engineered for your success. (online.uc.edu)
- The profession is expected to grow 7% by 2028, a bit faster than the national average. (wgu.edu)
- 100% of the courses are offered online, and no campus visits are required — a big time-saver for you. (online.uc.edu)
- As of 2020, personal bankers or tellers make an average of $32,620 per year, according to the BLS. (wgu.edu)
External Links
How To
How do you apply the Kaizen method to your life?
Kaizen means continuous improvement. This Japanese term refers to the Japanese philosophy of continuous improvement that emphasizes incremental improvements and constant improvement. It is a process where people come together to improve their processes.
Kaizen is one of the most effective methods used in Lean Manufacturing. Kaizen is a concept where employees in charge of the production line are required to spot problems during the manufacturing process before they become major issues. This is how you can improve the quality and lower the cost.
The main idea behind kaizen is to make every worker aware of what happens around him/her. So that there is no problem, you should immediately correct it if something goes wrong. If someone is aware of a problem at work, he/she should inform his/her manager immediately.
Kaizen has a set of basic principles that we all follow. Start with the end product, and then move to the beginning. In order to improve our factory's production, we must first fix the machines producing the final product. Next, we fix the machines which produce components. We then fix the workers that work with those machines.
This method, called 'kaizen', focuses on improving each and every step of the process. Once we have finished fixing the factory, we return to the beginning and work until perfection.
It is important to understand how to measure the effectiveness and implementation of kaizen in your company. There are many ways to tell if kaizen is effective. Another method is to see how many defects are found on the products. Another way is to see how much productivity has increased since implementing kaizen.
Another way to know whether kaizen is working is to ask yourself why did you decide to implement kaizen. Did you do it because it was legal or to save money? You really believed it would make you successful?
Suppose you answered yes to any of these questions, congratulations! You're ready to start kaizen.