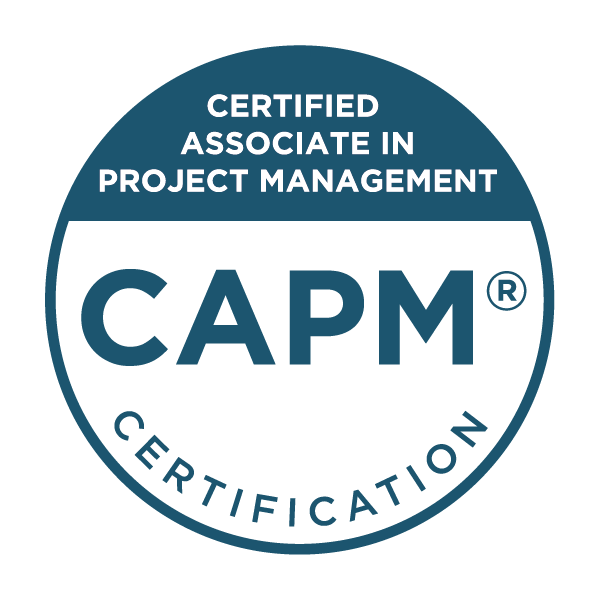
A certified construction manager is an experienced professional in the construction industry. To prove their competence, these professionals must pass a formal exam. This exam measures the candidate's knowledge in the field. The duration of the examination depends on the qualification. The average time it takes to pass is four hours.
Earnings potential
It can be lucrative to earn a degree in construction management. The education required is typically four years, although it is possible to earn a master's in construction management in as little as one year. A year of work experience will be required before you can begin your pursuit of certification.
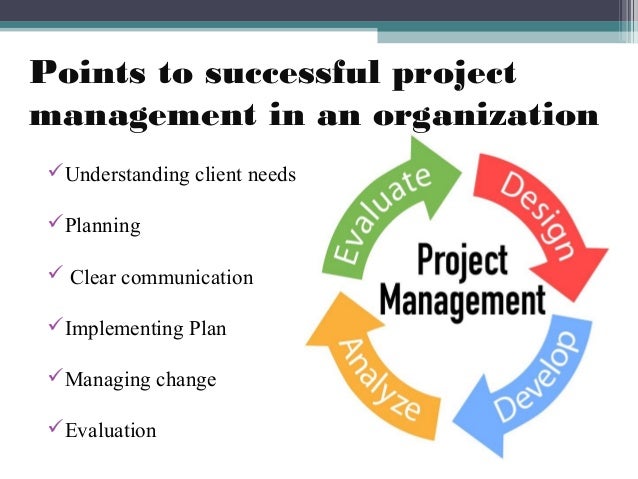
Earning a certificate as a construction manager can increase your earning power and help you keep all your certifications and licenses current. Certification courses can also help you stay current on safety and compliance guidelines.
Credentials required
Certification is a great way to increase your skills, whether you are looking to build a career as a construction manager or just to improve your resume. It can not only validate your commitment to the field but it can also help you get the job that you want quicker. There are many certifications you can get, and it is critical that you choose one that best suits your career goals.
To earn the credential you need to pass a six-hour, 200-question exam. This test tests your construction management and safety knowledge. After passing the test, you will be able to access a mentor directory and become Certified Construction Manager. The credential can be used for up to seven consecutive years after you have earned it. However, you will need to retake the exam every seven years.
Doing job
A construction manager is an individual with special knowledge in building construction. They work closely alongside civil engineers and other experts in building construction to complete a project. They manage and negotiate construction terms. They are responsible for selecting contractors and subcontractors. They may also interact with lawyers or local officials.
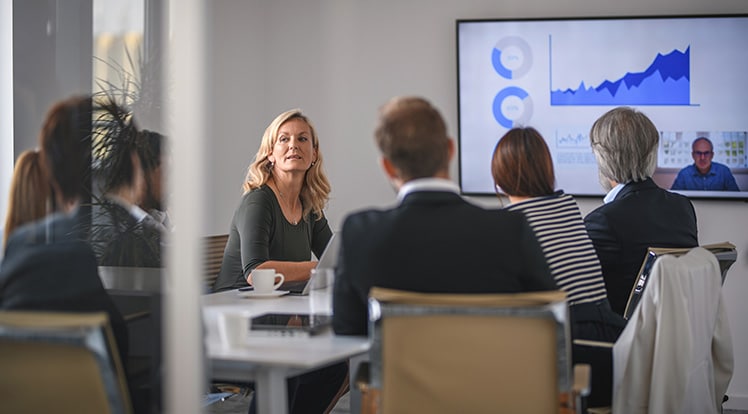
To ensure a successful construction project, construction managers must be capable of identifying and mitigating risks. A construction manager must also be able to work well with multiple teams in order to ensure that every aspect of the construction process is being done to the highest standard. This position typically requires a bachelor's in construction management and at least five years of relevant work experience. In order to successfully communicate with different audiences and solve problems and disputes, construction managers should have excellent communication skills.
FAQ
What kind of people use Six Sigma?
Six sigma is a common concept for people who have worked in statistics or operations research. Anybody involved in any aspect or business can benefit.
This requires a lot of dedication, so only people with great leadership skills can make the effort to implement it.
How do you effectively manage employees?
Effectively managing employees requires that you ensure their happiness and productivity.
It means setting clear expectations for them and keeping an eye on their performance.
To do this successfully, managers need to set clear goals for themselves and for their teams.
They need to communicate clearly with staff members. They also need to make sure that they discipline and reward the best performers.
They will also need to keep records about their team's activities. These include:
-
What did you accomplish?
-
How much work was put in?
-
Who did it all?
-
Was it done?
-
Why did it happen?
This information can help you monitor your performance and to evaluate your results.
How does Six Sigma work?
Six Sigma uses statistical analyses to locate problems, measure them, analyze root cause, fix problems and learn from the experience.
The first step to solving the problem is to identify it.
Next, data is collected and analyzed to identify trends and patterns.
Then, corrective actions can be taken to resolve the problem.
The data are then reanalyzed to see if the problem is solved.
This continues until you solve the problem.
What are the steps of the management decision-making process?
Managers face complex and multifaceted decision-making challenges. It involves many factors, including but not limited to analysis, strategy, planning, implementation, measurement, evaluation, feedback, etc.
The key thing to remember when managing people is that they are human beings just as you are and therefore make mistakes. You are always capable of improving yourself, and there's always room for improvement.
This video explains the process of decision-making in Management. We will explain the importance of different types decisions and how every manager can make them. Here are some topics you'll be learning about:
What is the difference in Six Sigma and TQM?
The major difference between the two tools for quality management is that six Sigma focuses on eliminating defect while total quality control (TQM), on improving processes and decreasing costs.
Six Sigma is an approach for continuous improvement. It emphasizes the elimination of defects by using statistical methods such as control charts, p-charts, and Pareto analysis.
This method attempts to reduce variations in product output. This is accomplished by identifying the root cause of problems and fixing them.
Total quality management involves measuring and monitoring all aspects of the organization. It also involves training employees to improve performance.
It is often used to increase productivity.
How does a manager learn to manage?
By practicing good management skills at all times.
Managers must constantly monitor the performance of their subordinates.
It is important to take immediate action if your subordinate doesn't perform as expected.
You should be able pinpoint what needs to improve and how to fix it.
Statistics
- The profession is expected to grow 7% by 2028, a bit faster than the national average. (wgu.edu)
- 100% of the courses are offered online, and no campus visits are required — a big time-saver for you. (online.uc.edu)
- This field is expected to grow about 7% by 2028, a bit faster than the national average for job growth. (wgu.edu)
- The average salary for financial advisors in 2021 is around $60,000 per year, with the top 10% of the profession making more than $111,000 per year. (wgu.edu)
- Your choice in Step 5 may very likely be the same or similar to the alternative you placed at the top of your list at the end of Step 4. (umassd.edu)
External Links
How To
How do you do the Kaizen method?
Kaizen means continuous improvement. The Japanese philosophy emphasizes small, incremental improvements to achieve continuous improvement. This term was created by Toyota Motor Corporation in 1950. It is a process where people come together to improve their processes.
Kaizen is one of Lean Manufacturing's most efficient methods. In this concept, employees who are responsible for the production line must identify problems that exist during the manufacturing process and try to solve them before they become big issues. This will increase the quality and decrease the cost of the products.
The main idea behind kaizen is to make every worker aware of what happens around him/her. Correct any errors immediately to avoid future problems. It is important that employees report any problems they see while on the job to their managers.
Kaizen is based on a few principles. When working with kaizen, we always start with the end result and move towards the beginning. In order to improve our factory's production, we must first fix the machines producing the final product. Then, we fix the machines that produce components and then the ones that produce raw materials. We then fix the workers that work with those machines.
This approach is called 'kaizen' because it focuses on improving everything steps by step. After we're done with the factory, it's time to go back and fix the problem.
Before you can implement kaizen into your business, it is necessary to learn how to measure its effectiveness. There are several ways that you can tell if your kaizen system is working. Another way to determine if kaizen is working well is to look at the quality of the products. Another way is determining how much productivity increased after implementing kaizen.
If you want to find out if your kaizen is actually working, ask yourself why. Was it just because it was the law or because you wanted to save money? It was a way to save money or help you succeed.
Let's say you answered yes or all of these questions. Congratulations! You are now ready to begin kaizen.