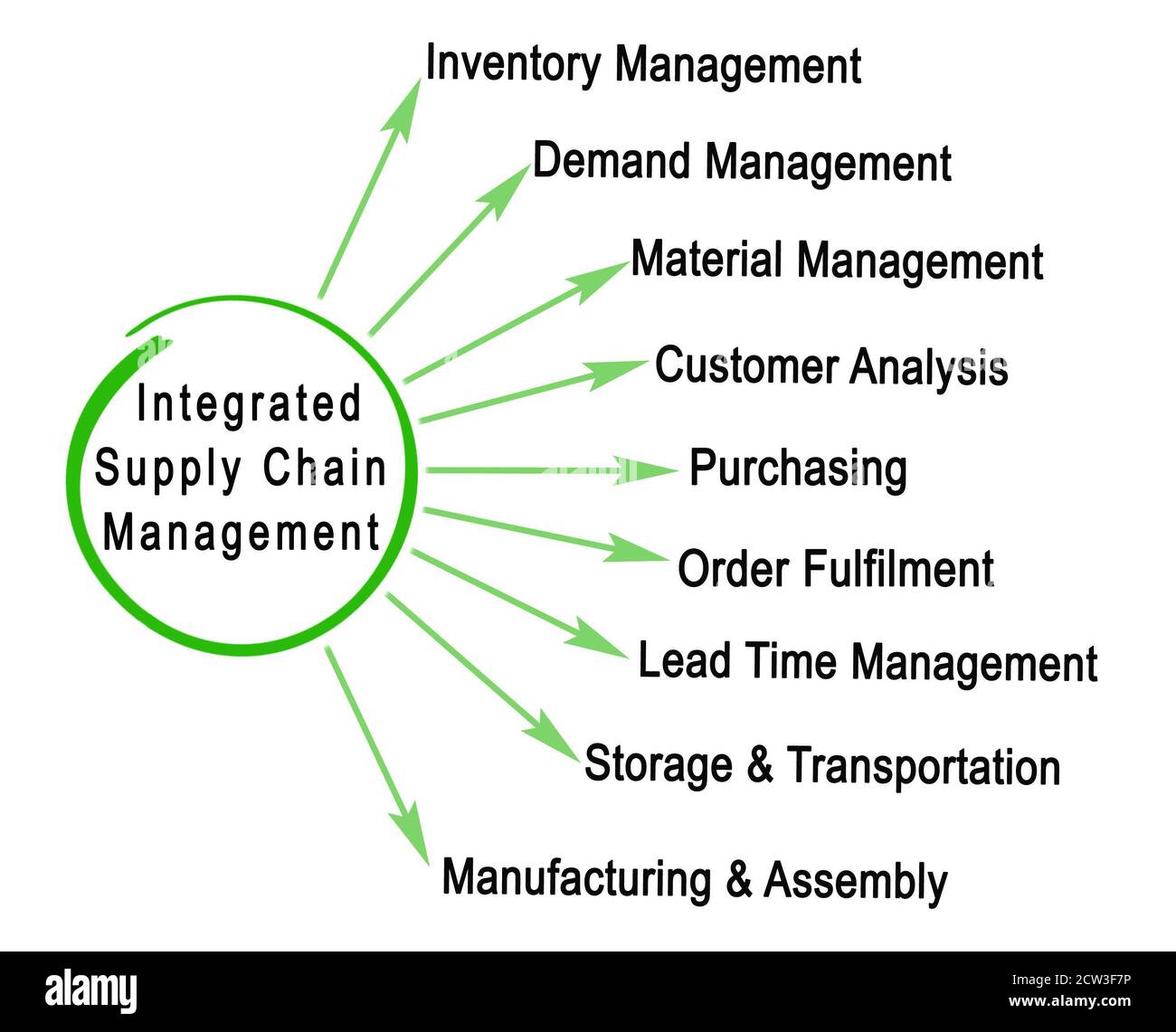
Woodland residents may have heard about the city's Waste Management contract. This company collects trash from homes, businesses, and other properties and recycles it. But what is this company actually doing? And why do so many people like it? Read on for more information. Founded in 1968, Waste Management (WM) is one of the nation's leading environmental services companies. Its mission: To protect the environment by reducing landfill waste.
Green Zone Recycling
The Green Zone Recycling Center in Woodland, California is a family-owned company. It is a subsidiary company of Recycling Solutions, Inc. The business is owned by Eric and Kim Jacobsen. Eric and Kim Jacobsen started Palletmasters as a full service pallet manufacturing firm in 1995. They then opened their first recycling center for customers in 2007. They support local charities and participate in community events. They have sponsored sports events and are a sponsor of schools in the community.
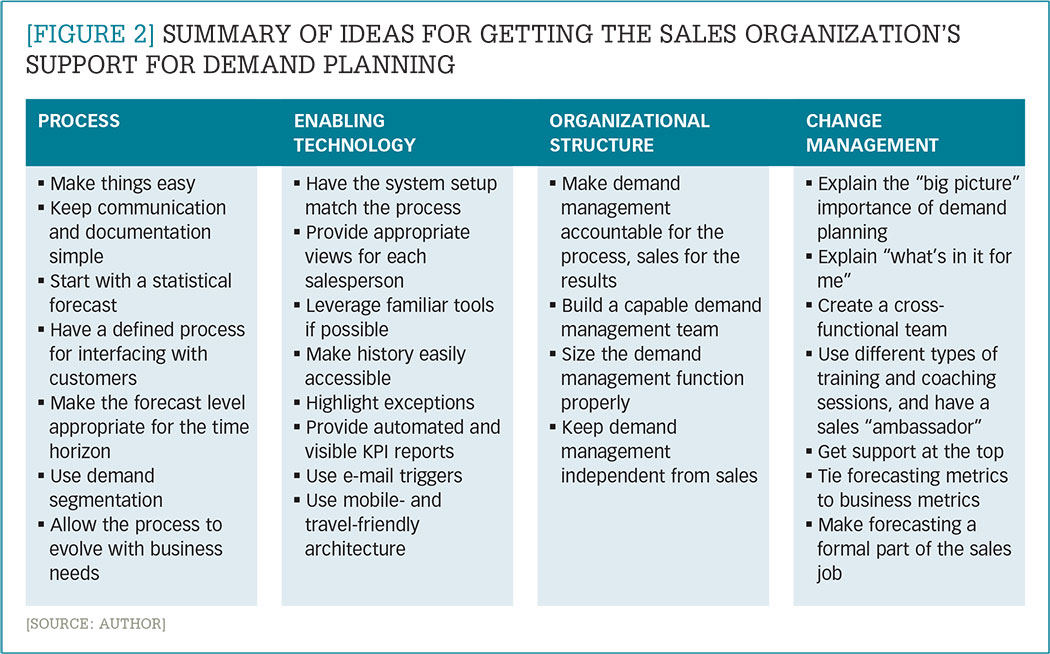
City of Woodland contracts with Waste Management
Woodland, Washington has had a long-standing agreement with Waste Management for residential garbage hauling. However, the city feels that Waste Management has violated this agreement by raising its rates. The city council voted in favor of reducing the rate increase to 56 cents per monthly through 2021. A Waste Management representative was also instructed by the council to request a delay. The city is currently investigating all possible alternatives to Waste Management.
City contracts with WM for trash collection
Waste Management Woodland collects trash for the City. It was established in 1968. They are an environmental management company and a waste management company. The company picks up garbage as well as yard and recyclable waste. They pride themselves in their environmental record and are committed to quality service. Waste Management is a subsidiary of the Waste Management Group.
City contracts with WM to pick up recyclables
Waste Management is contracted by the City of Woodland to collect recyclables from residents' homes. The company was established by Waste Management in 1968. It provides environmental and waste management services. They pick up paper, glass, metal, and other recyclables from households. Call 909-885-9000 to arrange a recycling pick up. They also pick up recyclables at other locations and businesses.
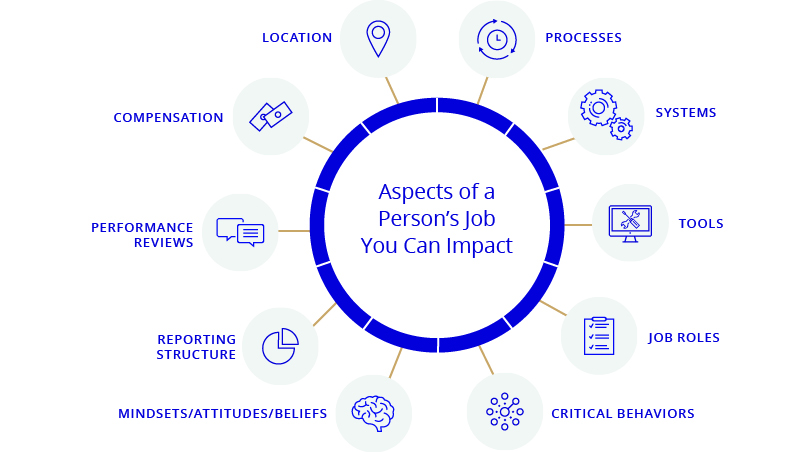
City contracts with WM for organic waste collection
The City recently signed a contract with Waste Management to pick up organic waste from residents and businesses. The new agreement will change waste rates and services. The new rates are expected to go into effect on November 1. Residents should expect to see some price increases, but those are minimal and should not cause alarm. Residents may receive notices by mail from the company. However, there is a way to reduce waste costs.
FAQ
How do you manage employees effectively?
The key to effective management of employees is ensuring their happiness and productivity.
It means setting clear expectations for them and keeping an eye on their performance.
Managers must be clear about their goals and those of their teams in order to succeed.
They need to communicate clearly and openly with staff members. They should also ensure that they both reward high performers and discipline those who are not performing to their standards.
They should also keep records of all activities within their team. These include:
-
What was achieved?
-
How much work was put in?
-
Who did it?
-
When it was done?
-
Why?
This information can be used to monitor performance and evaluate results.
What does "project management" mean?
This refers to managing all activities that are involved in a project's execution.
Our services include the definition of the scope, identifying requirements, preparing a budget, organizing project teams, scheduling work, monitoring progress and evaluating the results before closing the project.
Six Sigma is so well-known.
Six Sigma is simple to implement and can yield significant results. It provides a framework that allows for improvement and helps companies concentrate on what really matters.
How do you define Six Sigma?
People who have worked with statistics and operations research will usually be familiar with the concepts behind six sigma. Anybody involved in any aspect or business can benefit.
It requires high levels of commitment and leadership skills to be successful.
What are the three main management styles you can use?
There are three main management styles: participative, laissez-faire and authoritarian. Each style has its strengths and weaknesses. Which style do yo prefer? Why?
Authority - The leader is the one who sets the direction and expects everyone in the organization to follow it. This style is most effective when an organization is large, stable, and well-run.
Laissez-faire: The leader lets each person decide for themselves. This style works best when the organization is small and dynamic.
Participative – The leader listens and takes in ideas from all. This approach works best in small organizations where everyone feels valued.
What are the five management steps?
These five stages are: planning, execution monitoring, review and evaluation.
Setting goals for the future is part of planning. This includes setting goals for the future and defining what you want.
Execution is the actual execution of the plans. They must be followed by all parties.
Monitoring is a way to track progress towards your objectives. Monitoring should include regular reviews of performance against goals and budgets.
Every year, there are reviews. They are a chance to see if everything went smoothly during the year. If not there are changes that can be made to improve the performance next year.
After each year's review, evaluation occurs. It helps to identify what went well and what didn’t. It also provides feedback on the performance of people.
How does a manager learn to manage?
It is important to have good management skills.
Managers must constantly monitor the performance of their subordinates.
You should immediately take action if you see that your subordinate is not performing as well as you would like.
It is essential to know what areas need to be improved and how to do it.
Statistics
- As of 2020, personal bankers or tellers make an average of $32,620 per year, according to the BLS. (wgu.edu)
- 100% of the courses are offered online, and no campus visits are required — a big time-saver for you. (online.uc.edu)
- The average salary for financial advisors in 2021 is around $60,000 per year, with the top 10% of the profession making more than $111,000 per year. (wgu.edu)
- Your choice in Step 5 may very likely be the same or similar to the alternative you placed at the top of your list at the end of Step 4. (umassd.edu)
- Our program is 100% engineered for your success. (online.uc.edu)
External Links
How To
What is Lean Manufacturing?
Lean Manufacturing uses structured methods to reduce waste, increase efficiency and reduce waste. They were created in Japan by Toyota Motor Corporation during the 1980s. It was designed to produce high-quality products at lower prices while maintaining their quality. Lean manufacturing focuses on eliminating unnecessary steps and activities from the production process. It is composed of five fundamental elements: continuous improvement; pull systems, continuous improvements, just-in–time, kaizen, continuous change, and 5S. It is a system that produces only the product the customer requests without additional work. Continuous improvement means continuously improving on existing processes. Just-in–time refers when components or materials are delivered immediately to their intended destination. Kaizen is continuous improvement. This can be achieved by making small, incremental changes every day. Last but not least, 5S is for sort. These five elements are used together to ensure the best possible results.
Lean Production System
Six key concepts make up the lean manufacturing system.
-
Flow - focus on moving material and information as close to customers as possible;
-
Value stream mapping - Break down each stage in a process into distinct tasks and create an overview of the whole process.
-
Five S's, Sort, Set in Order, Shine. Standardize. and Sustain.
-
Kanban - visual cues such as stickers or colored tape can be used to track inventory.
-
Theory of constraints - identify bottlenecks during the process and eliminate them with lean tools like Kanban boards.
-
Just-in-time delivery - Deliver components and materials right to your point of use.
-
Continuous improvement - make incremental improvements to the process rather than overhauling it all at once.