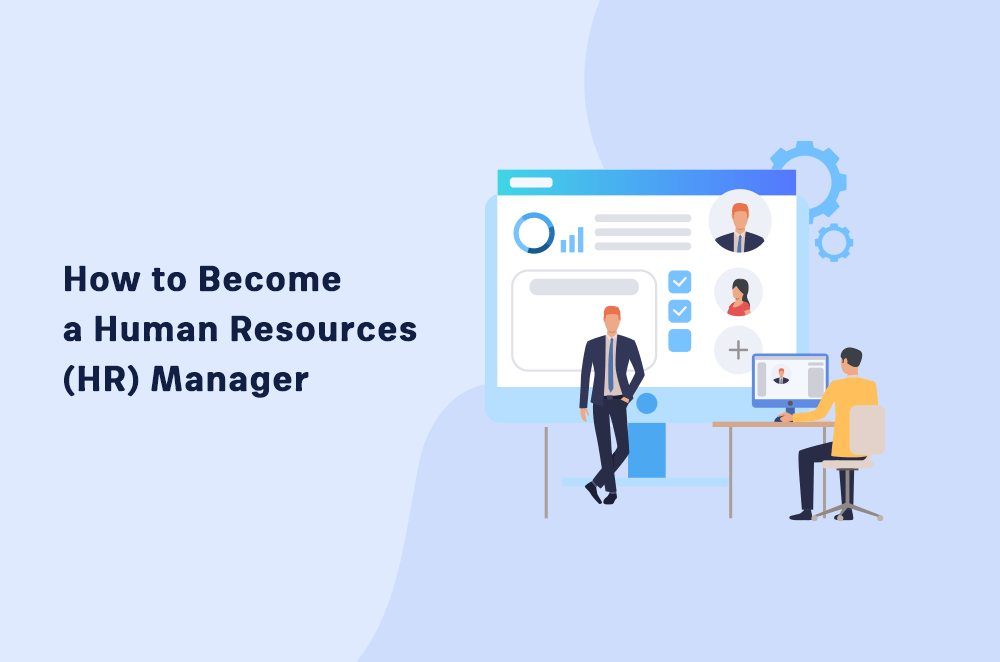
CSCMP is for Certified Systems and Communications Manager. It's a valuable certification for professionals in systems and communications. The CSCMP exam consists of 160 questions and takes four hours to complete. It is given by an independent 3rd-party company called Pearson VUE, and there are testing centers worldwide. The test is proctored in person and awards pass/fail status.
Academic membership
Academic membership is only available to full-time academic employees at accredited colleges and universities. Membership requires $175 annually and offers opportunities to develop course content and participate in collaborative forums. This membership allows members to meet other professionals in the field. For more information on how to become a member, contact us.
Membership fees
The Council of Supply Chain Management Professionals was established to connect, educate, and develop supply chain professionals all over the world. You can join the group for 6 months and get access to many member events and benefits. Young professionals can also sign up for a six-month membership for only $88. Both membership options are valid until August 31, 2021.
CSCMP members have access to all resources of the organization, including leading research and surveys. CSCMP members have first access to this research and other actionable insights. Members can also access webinars that are completely free. CSCMP members can find out more information about supply chain management as well as how to improve your business operations.
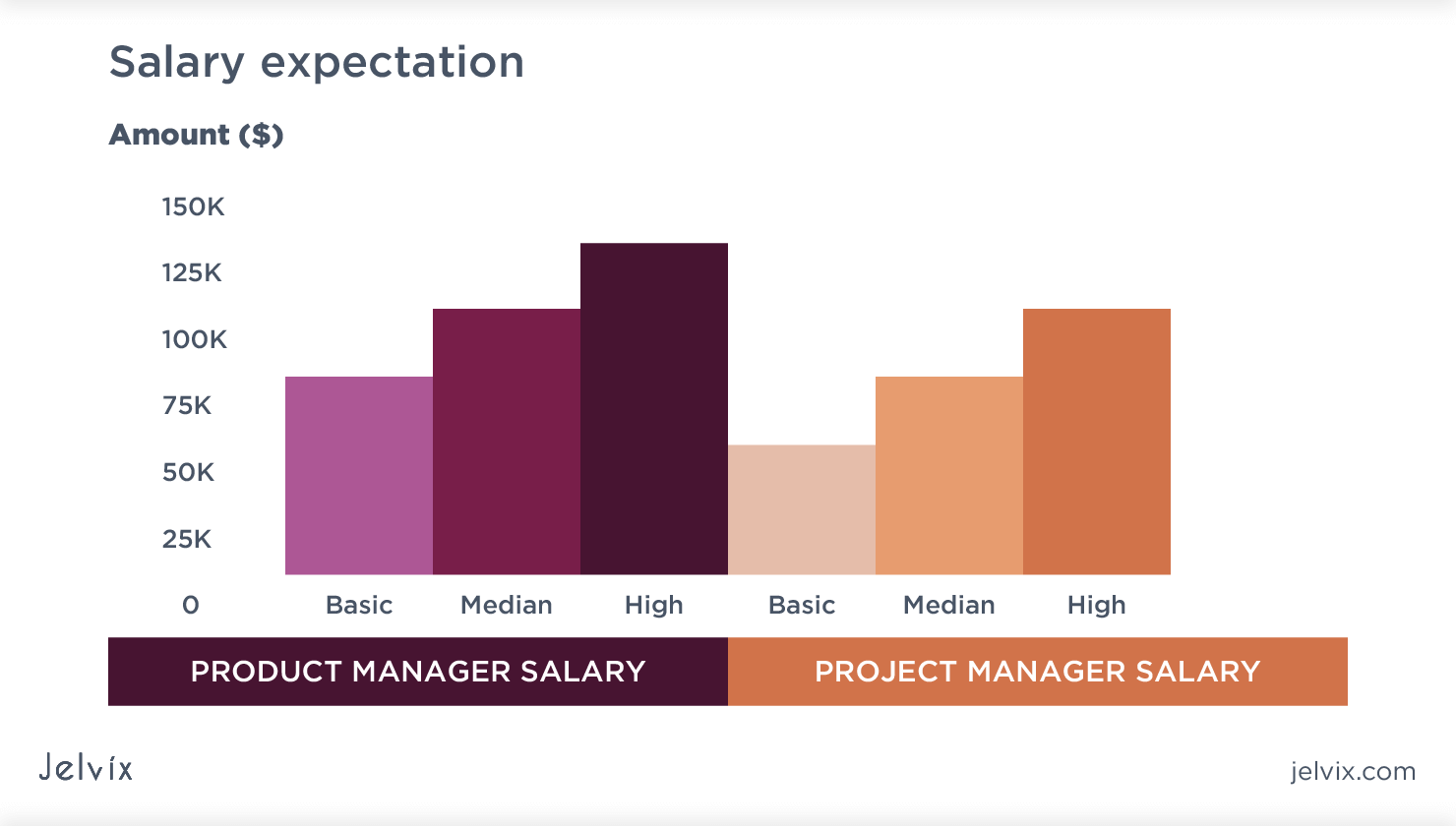
CSCMP members can be made by passing the SCMP Level 2 exam. The exam can be taken within one year after you submit your membership fee. You will be sent a confirmation email a week or so prior to your scheduled test date.
FAQ
What are the four main functions of management?
Management is responsible of planning, organizing, leading, and controlling people as well as resources. It includes the development of policies and procedures as well as setting goals.
Management helps an organization achieve its objectives by providing direction, coordination, control, leadership, motivation, supervision, training, and evaluation.
These are the four major functions of management:
Planning - Planning is about determining what must be done.
Organizing – Organizing means deciding how to organize things.
Direction - This is the art of getting people to follow your instructions.
Controlling - This is the ability to control people and ensure that they do their jobs according to plan.
Six Sigma is so popular.
Six Sigma is simple to implement and can yield significant results. It provides a framework that allows for improvement and helps companies concentrate on what really matters.
How can we create a successful company culture?
A positive company culture creates a sense of belonging and respect in its people.
It's based on three main principles:
-
Everyone has something to contribute
-
People are treated fairly
-
There is mutual respect between individuals and groups
These values are evident in the way that people act. They will show consideration and courtesy to others.
They will listen respectfully to the opinions of others.
And they will encourage others to share ideas and feelings.
Company culture also encourages open communication, collaboration, and cooperation.
People feel safe to voice their opinions without fear of reprisal.
They understand that mistakes can be forgiven as long as they're dealt with honestly.
Finally, the company culture promotes integrity and honesty.
Everyone understands that the truth is always best.
Everyone understands that there are rules and regulations which apply to them.
Nobody expects to be treated differently or given favors.
What are the 5 management processes?
The five stages of any business are planning, execution, monitoring, review, and evaluation.
Planning means setting goals for the long-term. This includes setting goals for the future and defining what you want.
Execution is when you actually execute the plans. They must be followed by all parties.
Monitoring is checking on progress towards achieving your objectives. Regular reviews of performance against targets, budgets, and other goals should be part.
Review events take place at each year's end. They allow for an assessment of whether all went well throughout the year. If not, then it may be possible to make adjustments in order to improve performance next time.
After the annual review is complete, evaluations are conducted. It helps identify which aspects worked well and which didn't. It also provides feedback on how well people performed.
What is the difference in leadership and management?
Leadership is all about influencing others. Management is about controlling others.
Leaders inspire others, managers direct them.
Leaders inspire people to achieve success. Managers keep their workers focused.
A leader develops people; a manager manages people.
What is the difference of a program and project?
A program is permanent, whereas a project is temporary.
A project typically has a defined goal and deadline.
It is often performed by a team of people, who report back on someone else.
A program usually has a set of goals and objectives.
It is typically done by one person.
Statistics
- Our program is 100% engineered for your success. (online.uc.edu)
- Hire the top business lawyers and save up to 60% on legal fees (upcounsel.com)
- UpCounsel accepts only the top 5 percent of lawyers on its site. (upcounsel.com)
- 100% of the courses are offered online, and no campus visits are required — a big time-saver for you. (online.uc.edu)
- This field is expected to grow about 7% by 2028, a bit faster than the national average for job growth. (wgu.edu)
External Links
How To
How can Lean Manufacturing be done?
Lean Manufacturing methods are used to reduce waste through structured processes. These processes were created by Toyota Motor Corporation, Japan in the 1980s. The aim was to produce better quality products at lower costs. Lean manufacturing seeks to eliminate unnecessary steps and activities in the production process. It consists of five basic elements: pull systems, continuous improvement, just-in-time, kaizen (continuous change), and 5S. Pull systems are able to produce exactly what the customer requires without extra work. Continuous improvement is the continuous improvement of existing processes. Just-in–time refers when components or materials are delivered immediately to their intended destination. Kaizen stands for continuous improvement. Kaizen can be described as a process of making small improvements continuously. Five-S stands for sort. It is also the acronym for shine, standardize (standardize), and sustain. These five elements can be combined to achieve the best possible results.
Lean Production System
Six key concepts form the foundation of the lean production system:
-
Flow - focus on moving material and information as close to customers as possible;
-
Value stream mapping - break down each stage of a process into discrete tasks and create a flowchart of the entire process;
-
Five S's – Sort, Put In Order Shine, Standardize and Sustain
-
Kanban is a visual system that uses visual cues like stickers, colored tape or stickers to keep track and monitor inventory.
-
Theory of constraints: identify bottlenecks in your process and eliminate them using lean tools, such as kanban board.
-
Just-intime - Order components and materials at your location right on the spot.
-
Continuous improvement - make incremental improvements to the process rather than overhauling it all at once.