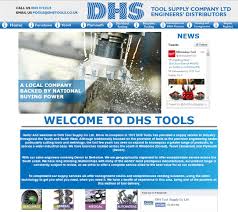
A webinar on supply chain can be a great way for you to find out more about current trends in your industry and how they affect your business. Many of these webinars are free and open for the public. You can find out more about Supply Chain Management as well as AI and Machine Learning. Some even touch on Industry 4.0 technologies and Multiparty control towers. These free events are great for business leaders or anyone just interested in learning more about supply chain technology.
Machine Learning
Machine Learning can be used in many ways throughout your supply chain. For example, it can optimize factory schedules, balance build-to-order and made-to-stock workflows, and prevent material delays during production. Machine learning can also help detect fraud. It analyses real-time data, looking for patterns and anomalies. Supply chain managers are notified of any problems.

AI
Predictive Analytics is a great tool to improve supply chain efficiency. But, it can be challenging to interpret the data generated from this technology. This webinar will help supply-chain managers to understand the basics of AI, and how they can apply it to their businesses.
Industry 4.0 technologies
Digital supply chains, also known as Industry 4.0, have made a huge shift in the way that businesses conduct business. It's difficult to discern the competitive advantage of new technologies because of the rapid pace at which they are changing. This Capstone Webinar will discuss the key domains of change and the agents behind the transformation. This webinar will address many of the most frequently asked questions regarding key technologies.
Multiparty control towers
Multiparty control Towers are an essential part of the supply-chain ecosystem. They can automate repetitive tasks for companies and help them save time and money. Multiparty control towers can be a powerful tool when used in conjunction with orchestration platforms. These solutions can link all parts of the supply chain ecosystem. They provide a single source to truth for all those involved.
Collaboration throughout the supply chains
Collaboration within the supply network is becoming an increasingly popular strategy. It can deliver significant benefits to companies' bottom lines. Collaboration not only increases operational efficiency but can also foster innovation, risk management and greater innovation. There are some important aspects to remember when collaborating across horizontal and vertical dimensions.
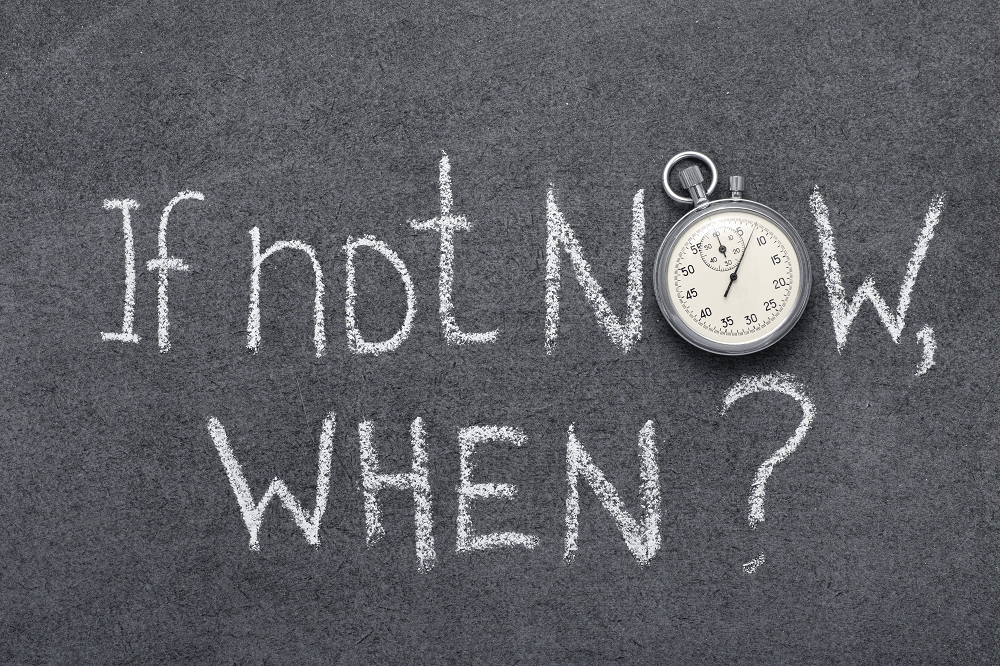
Future of the supply chain
Future of the supply chain webinars address the issues affecting supply chains. They address how to make them sustainable and integrate corporate governance into the value chains. They also discuss how to deal the increasing convergence in ESG and antitrust concerns. The session will focus on trends in supply chains starting in 2022, and continuing into the future.
FAQ
What are management theories?
Management concepts are the principles and practices used by managers to manage people, resources. These topics include job descriptions, performance evaluations and training programs. They also cover human resource policies, job description, job descriptions, job descriptions, employee motivation, compensation systems, organizational structures, and many other topics.
How to effectively manage employees
Managing employees effectively means ensuring that they are happy and productive.
This includes setting clear expectations for their behavior and tracking their performance.
Managers need to establish clear goals for their team and for themselves.
They should communicate clearly to staff members. They need to communicate clearly with their staff.
They must also keep track of the activities of their team. These include:
-
What was accomplished?
-
How much work was put in?
-
Who did it?
-
How did it get done?
-
Why?
This information can be used for monitoring performance and evaluating results.
Which kind of people use Six Sigma
Six Sigma is well-known to those who have worked in operations research and statistics. Anyone involved in business can benefit.
Because it requires a high level of commitment, only those with strong leadership skills will make an effort necessary to implement it successfully.
What is a management tool to help with decision-making?
A decision matrix, a simple yet powerful tool for managers to make decisions, is the best. It helps them to think strategically about all options.
A decision matrix can be used to show alternative options as rows or columns. This allows one to see how each alternative impacts other options.
This example shows four options, each represented by the boxes on either side of the matrix. Each box represents one option. The status quo (the current condition) is shown in the top row, and what would happen if there was no change?
The effect of Option 1 can be seen in the middle column. This would result in an increase of sales of $2 million to $3million.
The results of choosing Option 2 and 3 can be seen in the columns below. These positive changes result in increased sales of $1 million and $500,000. But, they also have some negative consequences. For instance, Option 2 increases cost by $100 thousand while Option 3 reduces profits by $200 thousand.
The final column shows results of choosing Option 4. This involves decreasing sales by $1 million.
A decision matrix has the advantage that you don’t have to remember where numbers belong. You just look at the cells and know immediately whether any given a choice is better than another.
This is because the matrix has already taken care of the hard work for you. It is as simple a matter of comparing all the numbers in each cell.
Here's a sample of how you might use decision matrixes in your business.
Advertising is a decision that you make. This will allow you to increase your revenue by $5000 per month. But, you will also incur additional expenses of $10 thousand per month.
By looking at the cell just below "Advertising", the net result can be calculated as $15 thousand. Advertising is more valuable than its costs.
What is the difference between TQM and Six Sigma?
The key difference between the two quality management tools is that while six-sigma focuses its efforts on eliminating defects, total quality management (TQM), focuses more on improving processes and reducing cost.
Six Sigma can be described as a strategy for continuous improvement. This approach emphasizes eliminating defects through statistical methods like control charts, Pareto analysis, and p-charts.
This method attempts to reduce variations in product output. This is done by identifying and correcting the root causes of problems.
Total quality management is the measurement and monitoring of all aspects within an organization. It also involves training employees to improve performance.
It is often used to increase productivity.
What is the difference between a project and a program?
A program is permanent, whereas a project is temporary.
A project is usually defined by a clear goal and a set deadline.
It is often carried out by a team of people who report back to someone else.
A program will usually have a set number of goals and objectives.
It is often implemented by one person.
Statistics
- The average salary for financial advisors in 2021 is around $60,000 per year, with the top 10% of the profession making more than $111,000 per year. (wgu.edu)
- Our program is 100% engineered for your success. (online.uc.edu)
- As of 2020, personal bankers or tellers make an average of $32,620 per year, according to the BLS. (wgu.edu)
- Your choice in Step 5 may very likely be the same or similar to the alternative you placed at the top of your list at the end of Step 4. (umassd.edu)
- 100% of the courses are offered online, and no campus visits are required — a big time-saver for you. (online.uc.edu)
External Links
How To
How can Lean Manufacturing be done?
Lean Manufacturing methods are used to reduce waste through structured processes. They were developed by Toyota Motor Corporation in Japan during the 1980s. It was designed to produce high-quality products at lower prices while maintaining their quality. Lean manufacturing emphasizes removing unnecessary steps from the production process. It is made up of five elements: continuous improvement, continuous improvement, just in-time, continuous change, and 5S. It is a system that produces only the product the customer requests without additional work. Continuous improvement refers to continuously improving existing processes. Just-in time refers to components and materials being delivered right at the place they are needed. Kaizen means continuous improvement. Kaizen involves making small changes and improving continuously. Five-S stands for sort. It is also the acronym for shine, standardize (standardize), and sustain. To achieve the best results, these five elements must be used together.
Lean Production System
Six key concepts form the foundation of the lean production system:
-
Flow - focus on moving material and information as close to customers as possible;
-
Value stream mapping - break down each stage of a process into discrete tasks and create a flowchart of the entire process;
-
Five S's, Sort, Set in Order, Shine. Standardize. and Sustain.
-
Kanban – visual signals like colored tape, stickers or other visual cues are used to keep track inventory.
-
Theory of Constraints - Identify bottlenecks in the process, and eliminate them using lean tools such kanban boards.
-
Just-intime - Order components and materials at your location right on the spot.
-
Continuous improvement - Make incremental improvements rather than overhauling the entire process.