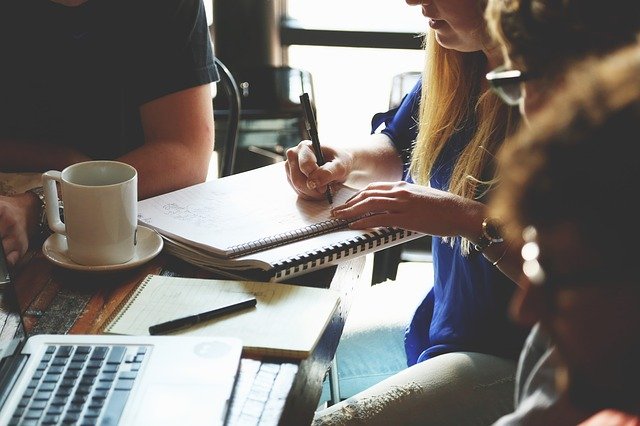
Although it can be difficult for teams to adopt a self-managed approach, they can be very beneficial. Continue reading to learn more about the benefits and disadvantages of self managed teams and how to incorporate them into your team. You will be able, after reading this article to decide if self-managed teams is right for you. Continue reading if you aren’t convinced.
Disadvantages of self-managed teams
There are many benefits and drawbacks to having self-managed business teams. Structures allow for greater flexibility, but they can also create a power vacuum within your team. Some people will assume the leadership position, while others may shirk their duties. Moreover, self-managed teams are not accountable to their management. It is difficult for managers to influence the team. This can lead to a decrease in productivity and creativity.
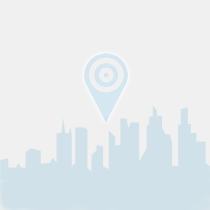
Self-managed organizations can have the disadvantage of being ineffective in enhancing organizational performance. Managers need to clearly communicate their roles and delegate authority to enable these teams to function well. In addition, self-managed teams can fail to meet the objectives set by their managers. Therefore, self-managed teams should have a manager who holds the team accountable for results and provides coaching and feedback to team members.
Challenges of self-managed teams
There are many benefits to self-managed groups. These teams tend to be more efficient than traditional teams, able to discuss ideas quickly and take action. These teams are more likely to be innovative as they assume responsibility for their own work. There are also some drawbacks. Self-managed teams might be better for some organizations but it is still important to think about them before making a decision. We'll be looking at the challenges and benefits of self-managed team.
A self-managed team may not only improve team productivity, but it can also be a challenge to individual commitment. A lot of members in self-directed teams are specialists in one task. This can cause problems with collaboration and shared commitment. This problem can be alleviated by establishing a system in which team members can vote on a decision and agree on a course of action. Because of the lack communication between teams, self-managed teams might not be as collaborative and productive as traditional teams.
Methods to manage your own teams
A culture of accountability is one way to create self-managed teams. In contrast to traditional teams, which have members taking full responsibility for their decisions, self managed teams are driven primarily by member commitments. Because each member recognizes both his or her individual responsibilities, this makes it easier for the work to move forward. This sense of accountability is emphasized throughout the entire team. This environment of accountability creates an environment that fosters creativity and innovation.
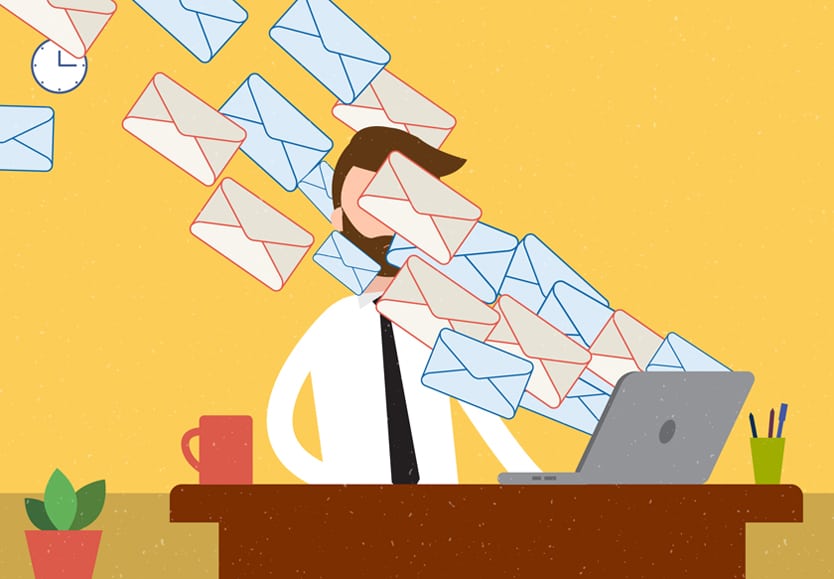
The first step in creating a self-managed team is to set up clear goals and tasks. You can set clear metrics for the team to measure its progress. You might be able to lead the industry's net promoter scores. If the self-managed team is new, you may have to hire new members to ensure success. You may also want to train employees in self-managed groups to make sure they are aware of the changes.
FAQ
How does Six Sigma work?
Six Sigma uses statistical analysis for problems to be found, measured, analyzed root causes, corrected, and learned from.
The first step in solving a problem is to identify it.
The data is then analyzed and collected to identify trends.
Then, corrective actions can be taken to resolve the problem.
Finally, data will be reanalyzed to determine if there is an issue.
This cycle will continue until the problem is solved.
What is a management tool to help with decision-making?
A decision matrix, a simple yet powerful tool for managers to make decisions, is the best. It allows them to consider all possible solutions.
A decision matrix is a way to organize alternatives into rows and columns. This makes it easy to see how each alternative affects other choices.
In this example, there are four possible options represented by boxes on the left-hand side of the matrix. Each box represents an option. The top row depicts the current status quo, while the bottom row represents what would happen if no action was taken.
The middle column displays the impact of selecting Option 1. In this example, it would lead to an increase in sales of between $2 million and $3 million.
The next two columns show the effects of choosing Options 2 and 3. These are both positive changes that increase sales by $1million and $500,000. They also have negative consequences. Option 2 increases costs by $100 thousand, while Option 3 decreases profits to $200 thousand.
The last column displays the results of selecting Option 4. This results in a decrease of sales by $1,000,000
The best part about using a decision matrix to guide you is that you don’t need to keep track of which numbers go where. Simply look at the cells to instantly determine if one choice is better than the other.
This is because your matrix has already done the hard work. It's simply a matter of comparing the numbers in the relevant cells.
Here's an example of how you might use a decision matrix in your business.
You need to decide whether to invest in advertising. If you do, you'll be able to increase your revenue by $5 thousand per month. However, additional expenses of $10 000 per month will be incurred.
If you look at the cell that says "Advertising", you can see the number $15,000. Advertising is more valuable than its costs.
Six Sigma is so well-known.
Six Sigma is easy and can deliver significant results. Six Sigma provides a framework to measure improvements and allows companies to focus on the most important things.
What is Six Sigma and how can it help you?
It is a way to improve quality that places emphasis on customer service and continuous learning. The goal is to eradicate defects through statistical techniques.
Motorola invented Six Sigma in 1986 as part its efforts to improve manufacturing.
The idea spread quickly throughout the industry, and today, many organizations are using six sigma methods to improve product design, production, delivery, and customer service.
Statistics
- Your choice in Step 5 may very likely be the same or similar to the alternative you placed at the top of your list at the end of Step 4. (umassd.edu)
- Hire the top business lawyers and save up to 60% on legal fees (upcounsel.com)
- Our program is 100% engineered for your success. (online.uc.edu)
- This field is expected to grow about 7% by 2028, a bit faster than the national average for job growth. (wgu.edu)
- UpCounsel accepts only the top 5 percent of lawyers on its site. (upcounsel.com)
External Links
How To
How can Lean Manufacturing be done?
Lean Manufacturing uses structured methods to reduce waste, increase efficiency and reduce waste. They were developed in Japan by Toyota Motor Corporation (in the 1980s). The primary goal was to make products with lower costs and maintain high quality. Lean manufacturing focuses on eliminating unnecessary steps and activities from the production process. It is made up of five elements: continuous improvement, continuous improvement, just in-time, continuous change, and 5S. The production of only what the customer needs without extra work is called pull systems. Continuous improvement means continuously improving on existing processes. Just-intime refers the time components and materials arrive at the exact place where they are needed. Kaizen is continuous improvement. This can be achieved by making small, incremental changes every day. Last but not least, 5S is for sort. These five elements can be combined to achieve the best possible results.
The Lean Production System
Six key concepts underlie the lean production system.
-
Flow is about moving material and information as near as customers can.
-
Value stream mapping - break down each stage of a process into discrete tasks and create a flowchart of the entire process;
-
Five S's – Sort, Put In Order Shine, Standardize and Sustain
-
Kanban is a visual system that uses visual cues like stickers, colored tape or stickers to keep track and monitor inventory.
-
Theory of constraints: Identify bottlenecks and use lean tools such as kanban boards to eliminate them.
-
Just-in time - Get components and materials delivered right at the point of usage;
-
Continuous improvement - incremental improvements are made to the process, not a complete overhaul.