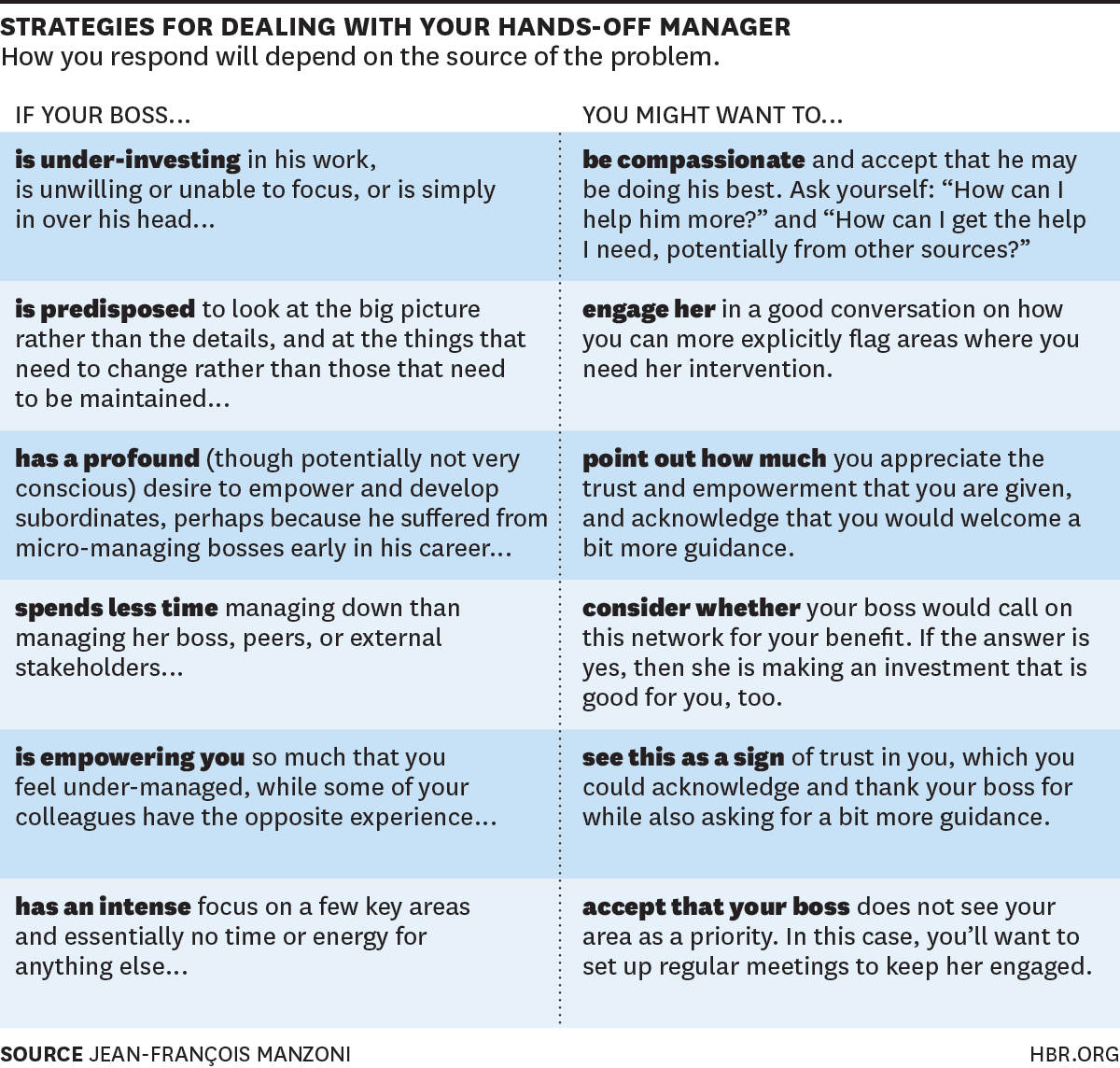
IT financial Management is the management of the financial activities of a business. It deals with the business's profitability, its expenses, cash flow, and credit flow. The goal is to ensure business growth and protect investors' financial interests. This article will provide an overview of IT financial Management. Here are some examples.
IT financial management is planning, organizing, directing and controlling the financial activities of a company
Financial management is a vital part of running a business. It's about managing a company’s finances. It also helps to plan its future. This includes making decisions on how to allocate profits and invest capital. These decisions affect how money is allocated to a company to meet its objectives. The financial manager is also responsible for ensuring that the company meets its tax obligations.
Often, financial management is about determining how a company will pay for day-to-day operations and expansion. A company might raise funds through private equity investments, sell assets, or issue stock. But before pursuing these options, a company must have enough cash to cover its day-to-day expenses and purchase raw materials. In addition, a company may introduce a new product that requires additional investment. The financial manager will need to assess the costs of the new product and determine the best source of funding.
It is strategic planning how a business should earn and spend money
The goal of financial management is to help business owners determine how to pay for the costs of running the business. This includes making decisions regarding raising capital, borrowing money, and creating and sticking to a budget. This involves analysing data in order to discover ways to improve business performance. It begins with recording all business income. After that, accountants create financial reports for the company, including balance sheets and cash flow statements as well as profit and loss statements.
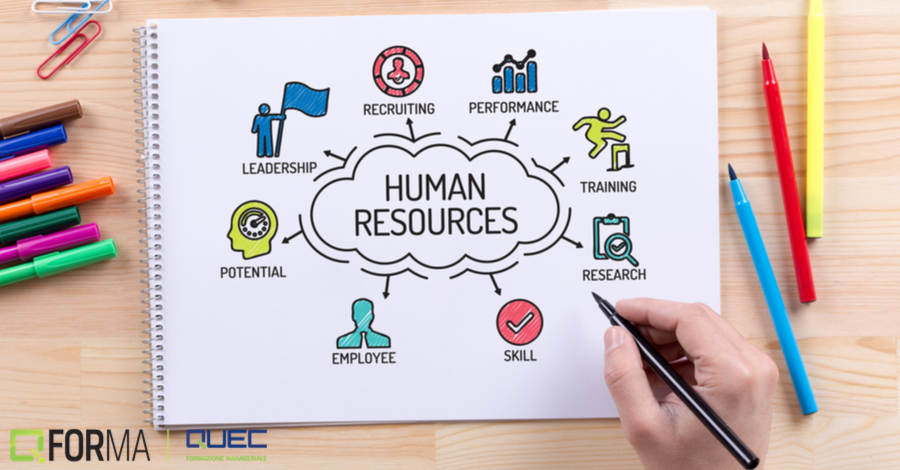
FAQ
How can we create a culture of success in our company?
Successful company culture is one where people feel valued and respected.
It's founded on three principal principles:
-
Everyone has something to contribute
-
Fair treatment of people is the goal
-
Respect is shared between individuals and groups
These values are reflected by the way people behave. They will show consideration and courtesy to others.
They will be respectful of the opinions of other people.
And they will encourage others to share ideas and feelings.
A company culture encourages collaboration and communication.
People feel free to express their views openly without fear of reprisal.
They know mistakes will be accepted as long as they are dealt with honestly.
The company culture encourages honesty and integrity.
Everyone knows that they must always tell the truth.
Everyone recognizes that rules and regulations are important to follow.
Everyone does not expect to receive special treatment.
What is Kaizen?
Kaizen, a Japanese term that means "continuous improvement," is a philosophy that encourages employees and other workers to continuously improve their work environment.
Kaizen is based on the belief that every person should be able to do his or her job well.
What kind people use Six Sigma?
Six Sigma will most likely be familiar to people who have worked in statistics and operations research. Anyone involved in business can benefit.
It is a commitment-intensive task that requires strong leadership skills.
Statistics
- This field is expected to grow about 7% by 2028, a bit faster than the national average for job growth. (wgu.edu)
- UpCounsel accepts only the top 5 percent of lawyers on its site. (upcounsel.com)
- The BLS says that financial services jobs like banking are expected to grow 4% by 2030, about as fast as the national average. (wgu.edu)
- The profession is expected to grow 7% by 2028, a bit faster than the national average. (wgu.edu)
- The average salary for financial advisors in 2021 is around $60,000 per year, with the top 10% of the profession making more than $111,000 per year. (wgu.edu)
External Links
How To
How is Lean Manufacturing done?
Lean Manufacturing uses structured methods to reduce waste, increase efficiency and reduce waste. These processes were created by Toyota Motor Corporation, Japan in the 1980s. The aim was to produce better quality products at lower costs. Lean manufacturing is about eliminating redundant steps and activities from the manufacturing process. It includes five main elements: pull systems (continuous improvement), continuous improvement (just-in-time), kaizen (5S), and continuous change (continuous changes). Pull systems are able to produce exactly what the customer requires without extra work. Continuous improvement involves constantly improving upon existing processes. Just-in–time refers when components or materials are delivered immediately to their intended destination. Kaizen means continuous improvement. Kaizen involves making small changes and improving continuously. The 5S acronym stands for sort in order, shine standardize and maintain. These five elements work together to produce the best results.
Lean Production System
Six key concepts form the foundation of the lean production system:
-
Flow - focuses on moving information and materials as close to customers as possible.
-
Value stream mapping - break down each stage of a process into discrete tasks and create a flowchart of the entire process;
-
Five S's, Sort, Set in Order, Shine. Standardize. and Sustain.
-
Kanban: Use visual signals such stickers, colored tape, or any other visual cues, to keep track your inventory.
-
Theory of constraints: identify bottlenecks in your process and eliminate them using lean tools, such as kanban board.
-
Just-intime - Order components and materials at your location right on the spot.
-
Continuous improvement is making incremental improvements to your process, rather than trying to overhaul it all at once.