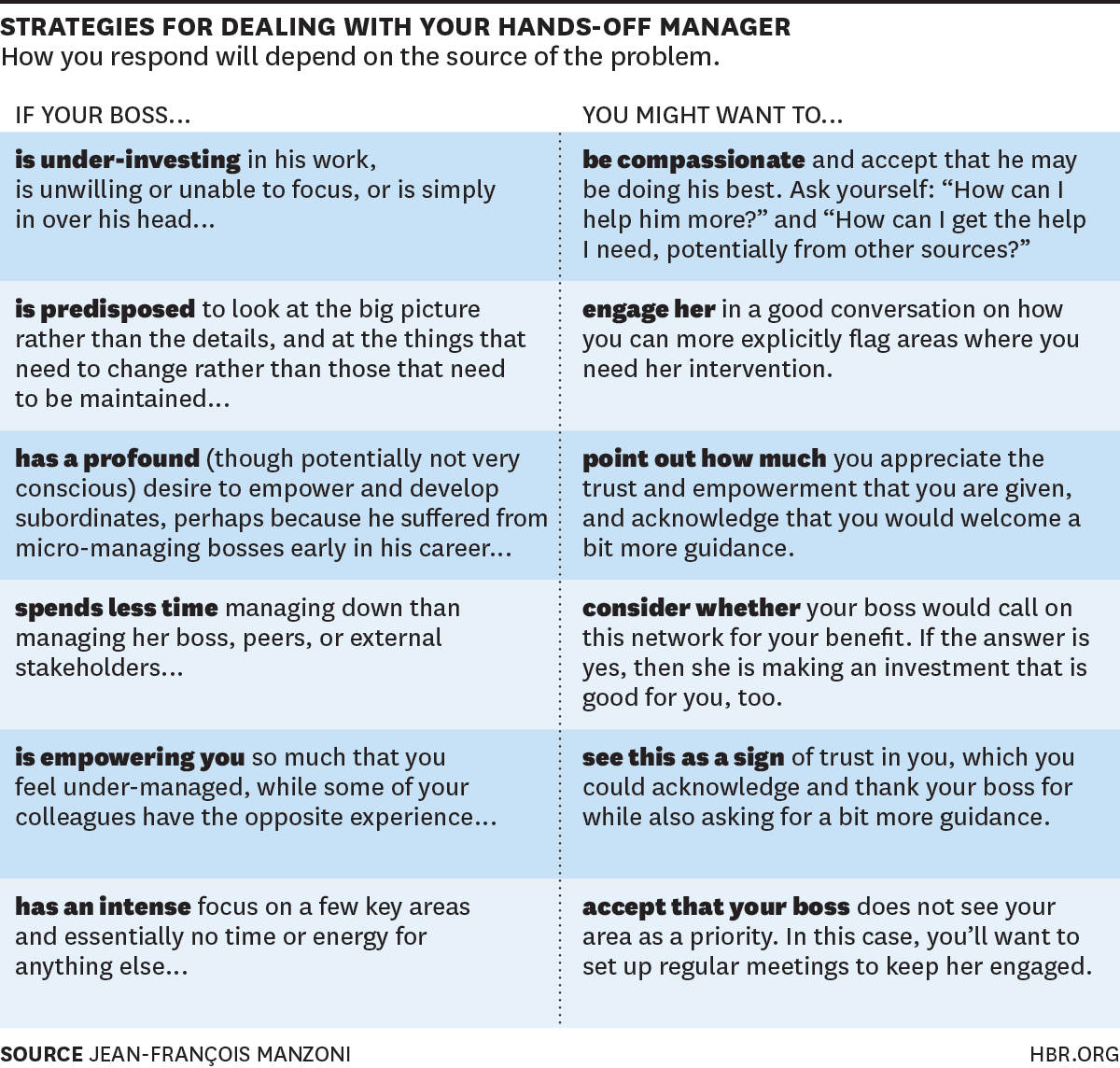
The Institute for Supply Management (ISM) is an organization that is dedicated to supply management. It publishes a monthly magazine and offers certification programs. The organization is non-profit with over 45,000 members. It has a strong reputation among supply chain managers and is the oldest association in the world. Its mission is to improve the business process through effective supply chain management. Visit its website to find out more about ISM.
ISM is a non-profit organization
The Institute of Supply Management, (ISM), is the oldest and most established supply management association in the globe. Its mission is to advance the practice and science of supply chain management. It extends its mission via education, research standards of excellence, information dissemination and standard-setting. More than 50,000 professionals from more than 80 countries are members of the organization. It offers several certifications, such as the Certified Professional in Purchasing Management and Certified Professional in Supplier Diversity.
The Institute of Supply Management is a non-profit organization that is dedicated to educating and supporting supply chain managers around the world. Its publications include Inside Supply Management, which debuted in June 1998. Its educational courses focus on all aspects of supply management, and it also includes a procurement curriculum.
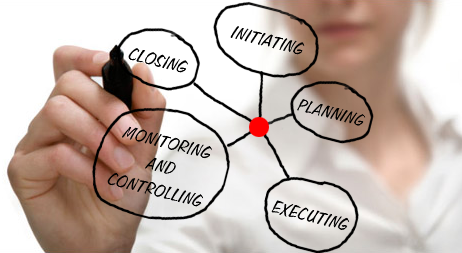
It also offers certification
The Institute for Supply Management offers CPSM certification for those who are interested in a career in procurement or supply chain management. This credential can be used by supply chain professionals worldwide. The credential is awarded to candidates who have met the requirements for academic and professional experience and passed three written exams.
The highest level of professional certification is CPSM. It validates your understanding of supply chain management functions. CPSM professionals need to have three years' experience working in a business that practices supply chain management and complete at least 60 hours of approved continuing education credits. Professionals with this certificate can be trusted to advise businesses on how to diversify their suppliers.
It publishes a magazine monthly
The Institute of supply management publishes both a newsletter, and a monthly publication. These publications are intended to be a valuable resource and a valuable resource for supply managers. They include information about the latest trends as well as innovations. They are also accessible to anyone interested in the supply management field, as well as non-members.
Inside Supply Management magazine and newsletter is for supply chain management and procurement professionals. It offers thought leadership, in-depth articles, and the latest trends. It is designed for professionals of all levels. This magazine covers everything you need to know about sourcing, strategicsourcing, ebusiness, and much more. Along with its informative articles, this magazine offers a range of online education programs.
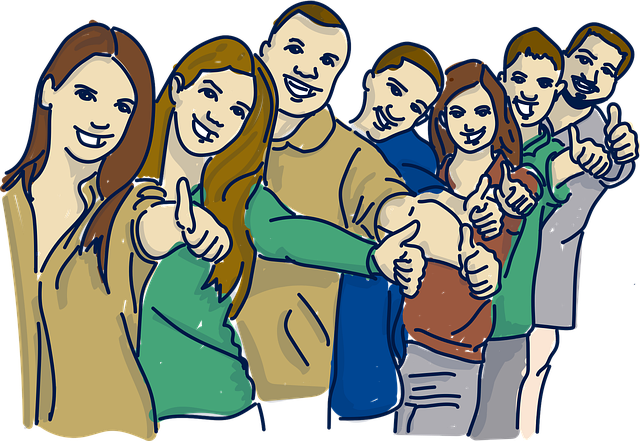
It also has a web site
The Institute of Supply Management is a non-profit organization that trains supply management professionals. The Institute of Supply Management was established in 1915. It provides education, certification, research, and support for the purchasing, supply, and logistics industries. The institute is a global association that has more than 50,000 members in 100 countries. It offers certifications and educational programs for supply-management professionals.
The ISM is the first non-profit supply management organization in the world. It uses cognitive computing and big-data to improve supply chain performance. Its certifications are designed to help supply management professionals grow in their careers while exposing them to new customer bases.
FAQ
What is the difference in leadership and management?
Leadership is about being a leader. Management is all about controlling others.
A leader inspires followers while a manager directs workers.
A leader motivates people to achieve success; a manager keeps workers on task.
A leader develops people; a manager manages people.
How do we create a company culture that is productive?
A culture of respect and value within a company is key to a productive culture.
It's founded on three principal principles:
-
Everyone has something to contribute
-
People are treated fairly
-
It is possible to have mutual respect between groups and individuals
These values can be seen in the behavior of people. They will treat others with respect and kindness.
They will listen respectfully to the opinions of others.
They can also be a source of inspiration for others.
A company culture encourages collaboration and communication.
People are free to speak out without fear of reprisal.
They know that they will not be judged if they make mistakes, as long as the matter is dealt with honestly.
Finally, the company culture promotes integrity and honesty.
Everyone is aware that truth must be told.
Everyone is aware that rules and regulations apply to them.
Nobody expects to be treated differently or given favors.
What's the difference between Six Sigma and TQM?
The key difference between the two quality management tools is that while six-sigma focuses its efforts on eliminating defects, total quality management (TQM), focuses more on improving processes and reducing cost.
Six Sigma is a method for continuous improvement. It emphasizes the elimination of defects by using statistical methods such as control charts, p-charts, and Pareto analysis.
This method seeks to decrease variation in product output. This is accomplished through identifying and correcting root causes.
Total quality management involves measuring and monitoring all aspects of the organization. It also includes training employees to improve performance.
It is often used to increase productivity.
Statistics
- The profession is expected to grow 7% by 2028, a bit faster than the national average. (wgu.edu)
- UpCounsel accepts only the top 5 percent of lawyers on its site. (upcounsel.com)
- 100% of the courses are offered online, and no campus visits are required — a big time-saver for you. (online.uc.edu)
- As of 2020, personal bankers or tellers make an average of $32,620 per year, according to the BLS. (wgu.edu)
- Our program is 100% engineered for your success. (online.uc.edu)
External Links
How To
How can you implement the Kaizen technique?
Kaizen means continuous improvement. The term was coined in the 1950s at Toyota Motor Corporation and refers to the Japanese philosophy emphasizing constant improvement through small incremental changes. It is a process where people come together to improve their processes.
Kaizen is one method that Lean Manufacturing uses to its greatest advantage. This concept requires employees to identify and solve problems during manufacturing before they become major issues. This is how you can improve the quality and lower the cost.
The main idea behind kaizen is to make every worker aware of what happens around him/her. So that there is no problem, you should immediately correct it if something goes wrong. If someone is aware of a problem at work, he/she should inform his/her manager immediately.
Kaizen has a set of basic principles that we all follow. When working with kaizen, we always start with the end result and move towards the beginning. For example, if we want to improve our factory, we first fix the machines that produce the final product. Next, we repair the machines that make components. Then, the machines that make raw materials. And finally, we fix the workers who work directly with those machines.
This is known as "kaizen", because it emphasizes improving each step. After we're done with the factory, it's time to go back and fix the problem.
Before you can implement kaizen into your business, it is necessary to learn how to measure its effectiveness. There are several ways to determine whether kaizen is working well. One method is to inspect the finished products for defects. Another way is determining how much productivity increased after implementing kaizen.
Another way to know whether kaizen is working is to ask yourself why did you decide to implement kaizen. Did you do it because it was legal or to save money? You really believed it would make you successful?
Congratulations if you answered "yes" to any of the questions. You are now ready to begin kaizen.