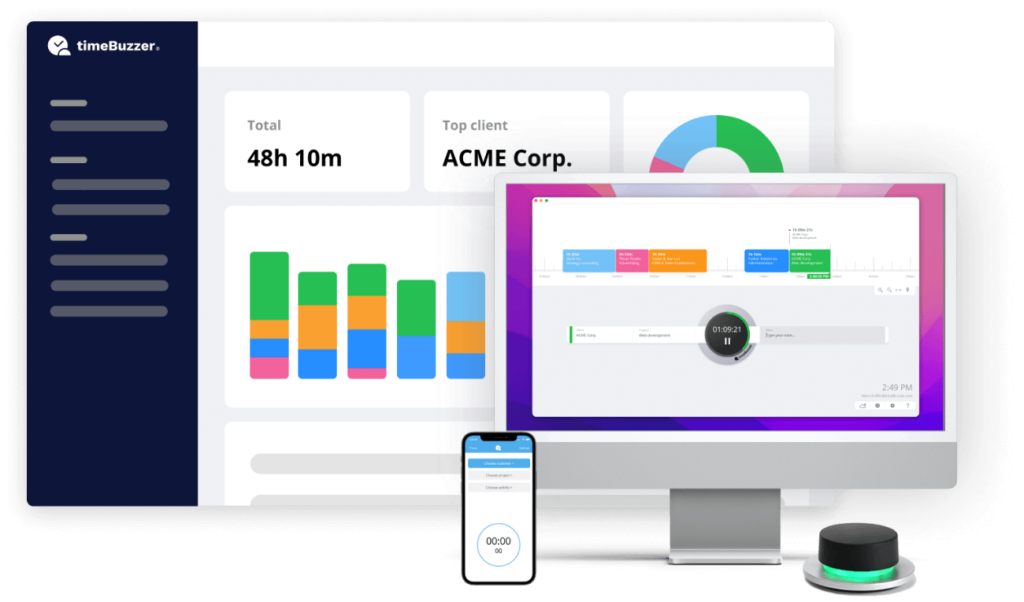
Business Process Reengineering or BPR is a methodology that allows cross functional teams to work together and identify and optimize business processes. It also helps companies collect and disseminate better data, which is crucial for sound improvements in customer service. BPR can also help organizations implement efficient business processes quicker and eliminate inefficient activities.
Taco Bell's experience with business process reengineering
Taco Bell’s business process reengineering program led directly to an increase in sales. The company's sales grew from less that 500 million in 1982 to more like $3 billion in ten years. They improved customer service and eliminated unnecessary paperwork. Additionally, the company was able to eliminate a lot of time that was spent on administration. This led to lower costs and increased employee morale.
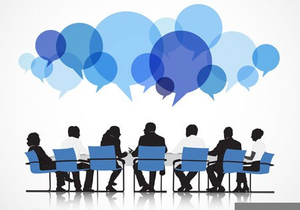
The new Defy drive through concept by Taco Bell, featuring a digital first experience, is one example of how Taco Bell has adapted for the digital revolution in food. This new concept was created to draw customers in a memorable way. The company also has a great branding opportunity with the concept. Although not every brand has the resources to invest in such an expensive project, it is possible for brands to redesign their offerings in order to offer more appealing customer experiences.
Another example is Taco Bell's innovative approach to mobile ordering. Taco Bell has partnered with Roadtrip Nation to create an online community where Taco Bell employees can share their experiences with others. This community allows employees to learn from one another, inspiring future team members.
Reengineering business processes has numerous benefits
Companies can improve efficiency and cut costs by performing business process redesign. Inefficient processes can cause delays in operations, which can lead to increased expenses and slow down the business. Reengineering business processes can improve the quality and quantity of services and products. This will increase customer satisfaction and boost the return-on-investment (ROI) of BPR initiatives.
Companies must give employees the tools and support they need to be successful in reengineering. This will improve employee happiness and customer satisfaction. Companies must also consider other factors when hiring workers. Workers must be able handle multiple tasks and be "Allrounders".
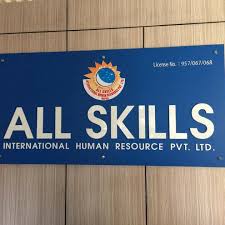
It is important to have a solid business case and strong staff buy-in before you start a BPR initiative. Successful implementation will require executive sponsorship. The right team must be able to offer their expertise. You may require a team that has a solid understanding of the business and its methodology. A good IT infrastructure is essential to facilitate process transformation.
FAQ
What is Six Sigma and how can it help you?
It is a way to improve quality that places emphasis on customer service and continuous learning. It is a method that eliminates defects using statistical techniques.
Six Sigma was developed at Motorola in 1986 as part of its efforts to improve manufacturing processes.
This idea quickly spread throughout the industry. Today, many organizations use six sigma methods for product design, production and delivery.
How does Six Sigma work?
Six Sigma uses statistical analysis to find problems, measure them, analyze root causes, correct problems, and learn from experience.
The first step in solving a problem is to identify it.
Next, data will be collected and analyzed to determine trends and patterns.
The problem can then be fixed by taking corrective measures.
Final analysis of data is done to determine if the problem has been solved.
This cycle will continue until the problem is solved.
What are the four major functions of Management?
Management is responsible to plan, organize, direct, and control people and resources. It includes the development of policies and procedures as well as setting goals.
Management is the ability to direct, coordinate, control, motivate, supervise, train, and evaluate an organization's efforts towards achieving its goals.
Management has four primary functions:
Planning - Planning is about determining what must be done.
Organizing: Organizing refers to deciding how things should work.
Directing - This refers to getting people follow instructions.
Controlling – This refers to ensuring that tasks are carried out according to plan.
What kind of people use Six Sigma
Six sigma is a common concept for people who have worked in statistics or operations research. But anyone can benefit from it.
This requires a lot of dedication, so only people with great leadership skills can make the effort to implement it.
What are management theories?
Management Concepts are the management principles and practices that managers use in managing people and resources. They cover topics like job descriptions (job descriptions), performance evaluations, training programmes, employee motivation and compensation systems.
What is the role of a manager in a company?
There are many roles that a manager can play in different industries.
In general, a manager controls the day-to-day operations of a company.
He/she will ensure that the company fulfills its financial obligations.
He/she ensures employees adhere to all regulations and quality standards.
He/she plans new products and services and oversees marketing campaigns.
What's the difference between a program and a project?
A program is permanent, whereas a project is temporary.
A project usually has a specific goal and deadline.
It is often done in a team that reports to another.
A program is usually defined by a set or goals.
It is typically done by one person.
Statistics
- Your choice in Step 5 may very likely be the same or similar to the alternative you placed at the top of your list at the end of Step 4. (umassd.edu)
- As of 2020, personal bankers or tellers make an average of $32,620 per year, according to the BLS. (wgu.edu)
- This field is expected to grow about 7% by 2028, a bit faster than the national average for job growth. (wgu.edu)
- Hire the top business lawyers and save up to 60% on legal fees (upcounsel.com)
- The BLS says that financial services jobs like banking are expected to grow 4% by 2030, about as fast as the national average. (wgu.edu)
External Links
How To
What is Lean Manufacturing?
Lean Manufacturing processes are used to reduce waste and improve efficiency through structured methods. They were developed by Toyota Motor Corporation in Japan during the 1980s. The primary goal was to make products with lower costs and maintain high quality. Lean manufacturing focuses on eliminating unnecessary steps and activities from the production process. It is made up of five elements: continuous improvement, continuous improvement, just in-time, continuous change, and 5S. The production of only what the customer needs without extra work is called pull systems. Continuous improvement refers to continuously improving existing processes. Just-in-time refers to when components and materials are delivered directly to the point where they are needed. Kaizen is continuous improvement. This can be achieved by making small, incremental changes every day. Five-S stands for sort. It is also the acronym for shine, standardize (standardize), and sustain. These five elements work together to produce the best results.
Lean Production System
Six key concepts form the foundation of the lean production system:
-
Flow - The focus is on moving information and material as close as possible to customers.
-
Value stream mapping: This is a way to break down each stage into separate tasks and create a flowchart for the entire process.
-
Five S’s - Sorted, In Order. Shine. Standardize. And Sustain.
-
Kanban – visual signals like colored tape, stickers or other visual cues are used to keep track inventory.
-
Theory of constraints - identify bottlenecks during the process and eliminate them with lean tools like Kanban boards.
-
Just-in Time - Send components and material directly to the point-of-use;
-
Continuous improvement is making incremental improvements to your process, rather than trying to overhaul it all at once.