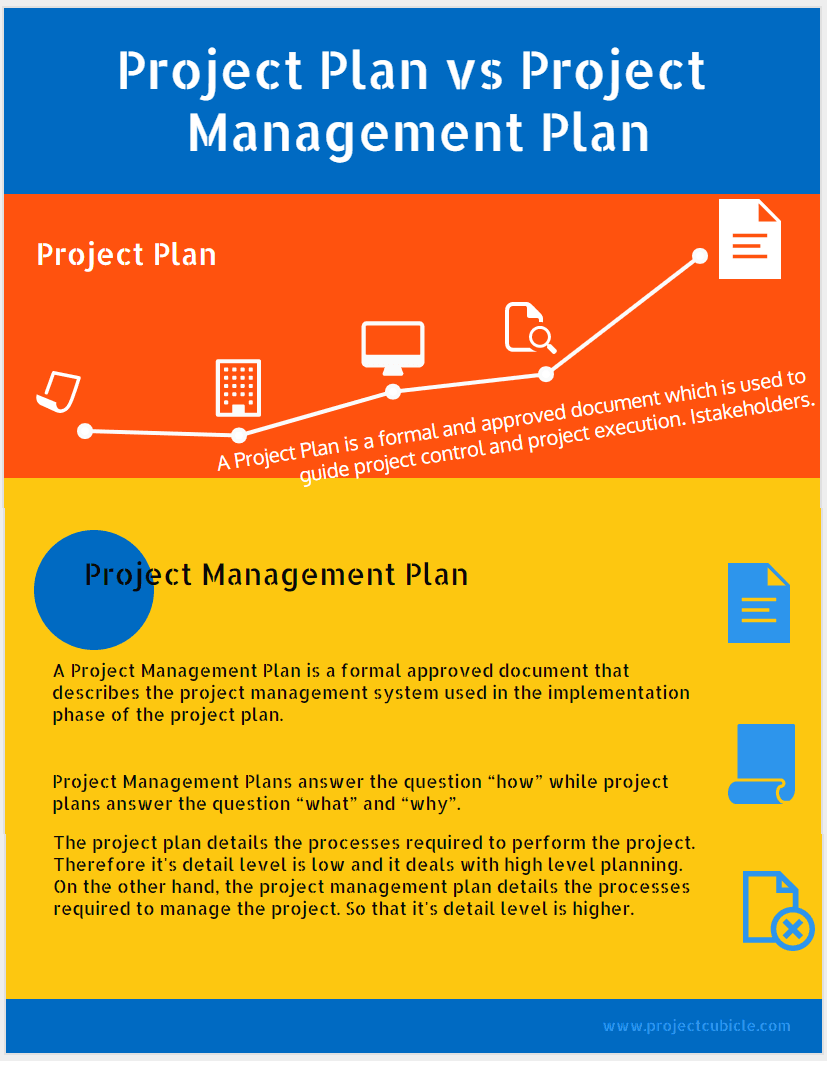
The key tool for quality and risk management is process knowledge management. It serves as a framework to link past and current knowledge, including data from products that are similar. It is also a foundation for continual improvement. Let's examine some of the advantages of process knowledge management. These are just a few of the benefits. It's possible to be very useful for your organization. It's also easy to put into practice.
Lessons learned
Your company should have a template that outlines the lessons learned. This template should be easily accessible by all employees. You can use a document management program to share your lessons with your employees if you don't have one. While the template should be easy to understand by your team members, it is worth testing other formats. The more complicated your document, the more likely your employees will resist sharing it. You must choose the most appropriate format to engage your staff.
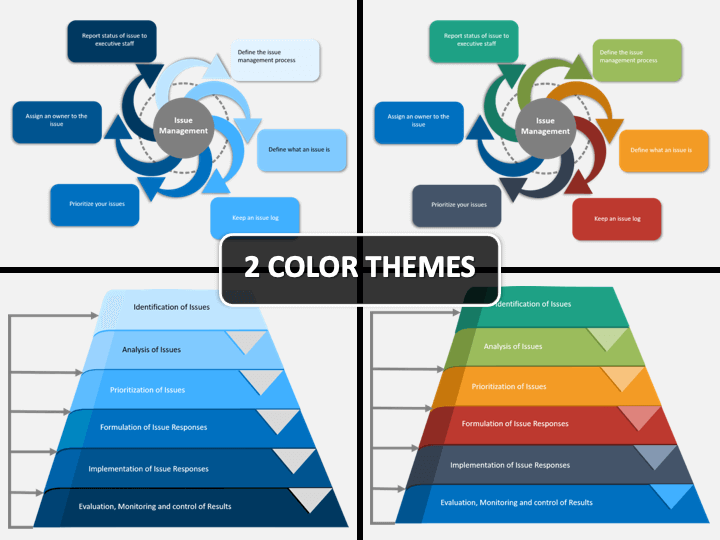
Expertise location
Expert location today is more than just biographical information. It allows you to share your knowledge and find the right employees to answer your questions. The majority of people have an account on LinkedIn, Facebook, Google+, or Google+ which includes their specific areas of expertise. These tools help to structure information and give people places to describe their projects as well as publications and knowledge. This can help to improve their image and reputation.
Communities and networks
The development of virtual community can foster cross-industry collaborations. These communities can foster communication and dissemination of new approaches, processes, and tools that help to improve performance and innovation in organisations. They can increase the effectiveness of meeting processes as well as disseminate cases histories. Industry leaders are investigating the many benefits of using community to improve industrial manufacturing. See Communities and networks for process knowledge management for more information. These networks provide a framework for knowledge management. They are meant to bring together people from different disciplines or locations.
Content management
While a content-management system can store a training document with 200 pages of information, it cannot replace a knowledge management system that can capture institutional and user-generated knowledge about a specific topic. A content-management system should allow for information to be captured from many perspectives. This will help in making better decisions and serving customers. For example, if a particular company is in the business of selling cars, a content-management system can store all of the dealership's sales training materials.
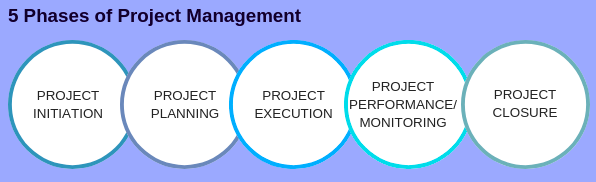
Knowledge mapping
Knowledge mapping can be a powerful tool to help you leverage your knowledge assets in order to improve your process. Knowledge mapping is a powerful way to identify knowledge gaps and find solutions for improving your process. It is also an excellent tool for increasing collaboration and engagement among departments. Once you have your knowledge mapped, you can work towards standardization of process. Knowledge maps are an excellent way to collect and disseminate best practice and improve your organization’s processes.
FAQ
What are some common mistakes managers make?
Sometimes managers make their job harder than they need to.
They may not delegate enough responsibilities to staff and fail to give them adequate support.
In addition, many managers lack the communication skills required to motivate and lead their teams.
Managers can set unrealistic expectations for their employees.
Some managers may try to solve every problem themselves instead of delegating responsibility to others.
What is TQM exactly?
The industrial revolution was when companies realized that they couldn't compete on price alone. This is what sparked the quality movement. If they wanted to stay competitive, they needed to improve their quality and efficiency.
Management realized the need to improve and created Total Quality Management, which focused on improving all aspects within an organization's performance. It included continuous improvement processes, employee involvement, and customer satisfaction.
What are the main four functions of management
Management is responsible in planning, organizing and directing people and resources. Management also involves setting goals and developing policies.
Management assists an organization in achieving its goals by providing direction, coordination and control, leadership, motivation, supervision and training, as well as evaluation.
The following are the four core functions of management
Planning - This is the process of deciding what should be done.
Organizing is the act of deciding how things should go.
Directing - This refers to getting people follow instructions.
Controlling - This is the ability to control people and ensure that they do their jobs according to plan.
What kind people use Six Sigma?
Six-sigma will be well-known to anyone who has worked in operations research or statistics. However, anyone involved in any aspect of business can benefit from using it.
Because it requires a high degree of commitment, only leaders with strong leadership skills can implement it successfully.
How do we build a culture that is successful in our company?
A culture of respect and value within a company is key to a productive culture.
It's founded on three principal principles:
-
Everybody can contribute something valuable
-
People are treated fairly
-
People and groups should respect each other.
These values are reflected in the way people behave. They will treat others with respect and kindness.
They will respect the opinions of others.
They will also encourage others to share their ideas and feelings.
The company culture promotes collaboration and open communication.
People are free to speak out without fear of reprisal.
They know that they will not be judged if they make mistakes, as long as the matter is dealt with honestly.
Finally, the company culture encourages honesty as well as integrity.
Everyone understands that the truth is always best.
Everyone recognizes that rules and regulations are important to follow.
Everyone does not expect to receive special treatment.
Statistics
- Our program is 100% engineered for your success. (online.uc.edu)
- 100% of the courses are offered online, and no campus visits are required — a big time-saver for you. (online.uc.edu)
- Hire the top business lawyers and save up to 60% on legal fees (upcounsel.com)
- The profession is expected to grow 7% by 2028, a bit faster than the national average. (wgu.edu)
- Your choice in Step 5 may very likely be the same or similar to the alternative you placed at the top of your list at the end of Step 4. (umassd.edu)
External Links
How To
How do you apply the Kaizen method to your life?
Kaizen means continuous improvement. Kaizen is a Japanese concept that encourages constant improvement by small incremental changes. It's a process where people work together to improve their processes continuously.
Kaizen, a Lean Manufacturing method, is one of its most powerful. The concept involves employees responsible for manufacturing identifying problems and trying to fix them before they become serious issues. This way, the quality of products increases, and the cost decreases.
Kaizen is the idea that every worker should be aware of what is going on around them. To prevent problems from happening, any problem should be addressed immediately. It is important that employees report any problems they see while on the job to their managers.
When doing kaizen, there are some principles we must follow. Start with the end product, and then move to the beginning. In order to improve our factory's production, we must first fix the machines producing the final product. Next, we repair the machines that make components. Then, the machines that make raw materials. We then fix the workers that work with those machines.
This method is known as kaizen because it focuses upon improving every aspect of the process step by step. Once we have finished fixing the factory, we return to the beginning and work until perfection.
It is important to understand how to measure the effectiveness and implementation of kaizen in your company. There are many methods to assess if kaizen works well. Another way to determine if kaizen is working well is to look at the quality of the products. Another method is to determine how much productivity has improved since the implementation of kaizen.
If you want to find out if your kaizen is actually working, ask yourself why. Did you do it because it was legal or to save money? Did you really believe it would lead to success?
Congratulations if you answered "yes" to any of the questions. You are ready to start kaizen.