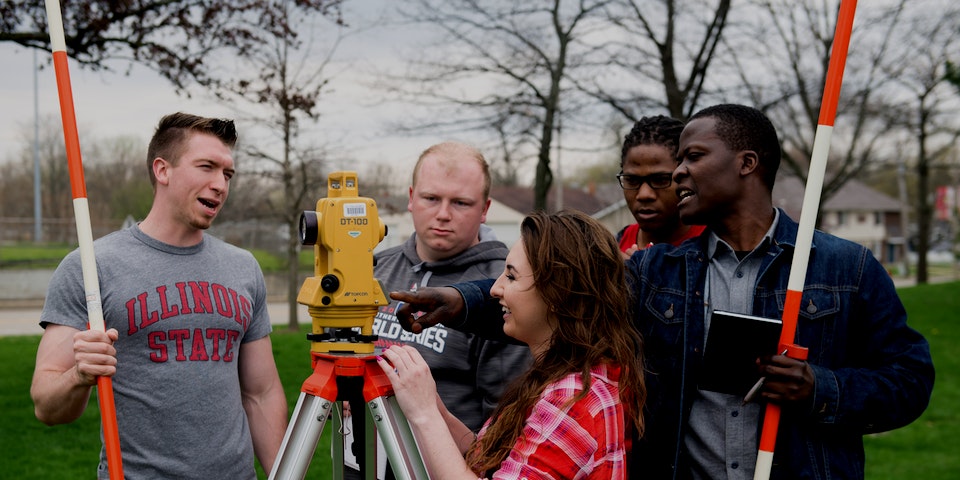
A degree that focuses exclusively on supply chain management is essential if you plan to pursue a career. You can take on the role of leader in a business by earning a degree in supply chain management. This includes operational, strategic, and tactical levels. It helps to improve organizational performance. It requires excellent communication skills.
Supply chain management can also include project management.
Supply chain management, which is essential for any business, is important. Project management can help improve the management of your supply chain. Project management is a process that helps you develop and implement a plan for your business. A project's primary objective is to produce a complete project that meets specified goals and other success criteria. The project manager also ensures that products and services are delivered on time and meet the quality standards you set. Project management offers many benefits, such as improved collaboration, cost-savings and quality control. There are also some drawbacks to project management.
Although tactics and strategy are important, they should not be implemented without proper planning. Without clear direction, strategies can go wrong and lead to projects that fail to reach their goals. A supply chain project's success depends on its project manager. Project managers can create solutions and implement new strategies by following best practices.
It can be at strategic, tactical and operational levels.
The three main levels of a supply chain are strategic, tactical and operational. Supply chain success is dependent on the strategic level. It sets the foundation for all levels. It involves analysing and collecting data and evaluating major factors that influence the supply chain. Then, it is necessary to make decisions based on this information. Although operational decisions are taken to satisfy customer requirements, strategic decisions are vital to the overall success and sustainability of the supply chain.
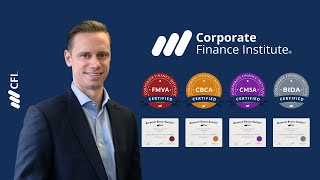
The strategic level describes the company's goals and strengths, as well as identifies weaknesses and formulates a vision for its future. Tactical level involves executing plans that achieve the strategy, with specific measures to meet them. These plans can include forecasting, inventory management, production scheduling, shipping, and invoicing. However, some analysts argue that the globalization and resulting in purely strategic functions has made tactical planning less important.
It can improve organizational performance
It is the ability of a supply chain manager to improve organizational performance that determines its effectiveness. Supply chain performance can be measured and evaluated through a variety of methods, including customer relationship management (CRM), internal supply chain management, and information sharing. These methods all contribute to improved organizational performance.
Supply chains are not all created equal. Some companies have never created a coherent supply chain structure. This results in single functions reporting to different parent functions, or even different points within a parent function. This can lead confusion and slow response time to critical issues. For example, demand planning processes may report to the supply-chain lead in one geography, but to sales leads in another. These organizational problems can result in significant inefficiencies.
It requires communication skills
To succeed in supply chain management, you need to have strong communication skills. Supply chain leaders should be able convey complex ideas and foster cooperation. Additionally, they should be able to produce accurate reports. Developing these skills will enhance your career prospects. If you want to work in supply chain management, consider furthering your education or pursuing certifications.
As a supply-chain manager, you will have to interact with many people. You will need to be able to listen and empathize with others. Your leadership skills may be reduced if you lack empathy, especially in times of change. Employees might feel devalued and rejected if you don't take the time to listen to their concerns. It is important to understand yourself better and improve your skills.
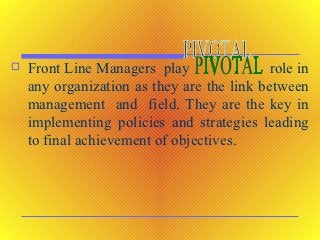
This can lead to a career as a supply chain manager.
A degree in supply management could open doors to many career options. Supply chain managers manage a wide range of processes, starting from the forecasting of consumer demand through to the finished product being placed on store shelves. The job involves managing an intricate network of people, vendors, and transportation systems. Supply chain managers must be well-versed in business management and computer science to be successful in the position.
You can either complete your degree in supply-chain management online or in the traditional classroom setting. Either way, you'll find your training to be comparable to a four-year program. Online programs tend to have fewer networking opportunities, but the quality of training is comparable to traditional schools. Strong analytical skills are required as well as a passion for forecasting and data analysis. An online degree program can help you teach technical aspects of supply chain administration to others.
FAQ
What's the difference between leadership & management?
Leadership is about being a leader. Management is about controlling others.
Leaders inspire followers, while managers direct workers.
Leaders inspire people to achieve success. Managers keep their workers focused.
A leader develops people; a manager manages people.
What are some common management mistakes?
Managers can make their jobs more difficult than necessary.
They may not assign enough responsibilities to staff members and provide them with inadequate support.
Many managers lack the communication skills to motivate and lead their employees.
Some managers set unrealistic expectations for their staff.
Managers may prefer to solve every problem for themselves than to delegate responsibility.
Why is Six Sigma so popular?
Six Sigma is easy to implement and can produce significant results. It provides a framework that allows for improvement and helps companies concentrate on what really matters.
How can we create a culture of success in our company?
A successful company culture is one that makes people feel valued and respected.
It's built on three fundamental principles:
-
Everybody has something to offer.
-
People are treated with respect
-
Respect is shared between individuals and groups
These values can be seen in the behavior of people. They will treat others with consideration and courtesy.
They will respect the opinions of others.
They will also encourage others to share their ideas and feelings.
Additionally, the company culture encourages open communication as well as collaboration.
People feel comfortable expressing their opinions freely without fear of reprisal.
They understand that errors will be tolerated as long they are corrected honestly.
Finally, the company culture promotes honesty and integrity.
Everybody knows they have to tell the truth.
Everyone knows that there are rules and regulations that apply to them.
People don't expect special treatment or favors.
What are the four main functions of management?
Management is responsible for organizing, managing, directing and controlling people, resources, and other activities. This includes setting goals, developing policies and procedures, and creating procedures.
Management helps an organization achieve its objectives by providing direction, coordination, control, leadership, motivation, supervision, training, and evaluation.
Management has four primary functions:
Planning - Planning is about determining what must be done.
Organizing: Organizing refers to deciding how things should work.
Directing - Directing means getting people to follow instructions.
Controlling - This is the ability to control people and ensure that they do their jobs according to plan.
What role can a manager fill in a company’s management?
Managers' roles vary from industry to industry.
Managers generally oversee the day-today operations of a business.
He/she makes sure that the company meets its financial obligations, and that it produces goods or services that customers desire.
He/she will ensure that employees follow all rules and regulations, and adhere to quality standards.
He/she plans new products and services and oversees marketing campaigns.
Statistics
- Hire the top business lawyers and save up to 60% on legal fees (upcounsel.com)
- Your choice in Step 5 may very likely be the same or similar to the alternative you placed at the top of your list at the end of Step 4. (umassd.edu)
- As of 2020, personal bankers or tellers make an average of $32,620 per year, according to the BLS. (wgu.edu)
- The profession is expected to grow 7% by 2028, a bit faster than the national average. (wgu.edu)
- 100% of the courses are offered online, and no campus visits are required — a big time-saver for you. (online.uc.edu)
External Links
How To
How does Lean Manufacturing work?
Lean Manufacturing methods are used to reduce waste through structured processes. They were developed in Japan by Toyota Motor Corporation (in the 1980s). It was designed to produce high-quality products at lower prices while maintaining their quality. Lean manufacturing seeks to eliminate unnecessary steps and activities in the production process. It has five components: continuous improvement and pull systems; just-in time; continuous change; and kaizen (continuous innovation). Pull systems are able to produce exactly what the customer requires without extra work. Continuous improvement refers to continuously improving existing processes. Just-intime refers the time components and materials arrive at the exact place where they are needed. Kaizen is continuous improvement. This can be achieved by making small, incremental changes every day. Five-S stands for sort. It is also the acronym for shine, standardize (standardize), and sustain. These five elements are combined to give you the best possible results.
Lean Production System
Six key concepts underlie the lean production system.
-
Flow is about moving material and information as near as customers can.
-
Value stream mapping is the ability to divide a process into smaller tasks, and then create a flowchart that shows the entire process.
-
Five S's – Sort, Put In Order Shine, Standardize and Sustain
-
Kanban - use visual signals such as colored tape, stickers, or other visual cues to keep track of inventory;
-
Theory of constraints - identify bottlenecks during the process and eliminate them with lean tools like Kanban boards.
-
Just-in-time - deliver components and materials directly to the point of use;
-
Continuous improvement is making incremental improvements to your process, rather than trying to overhaul it all at once.