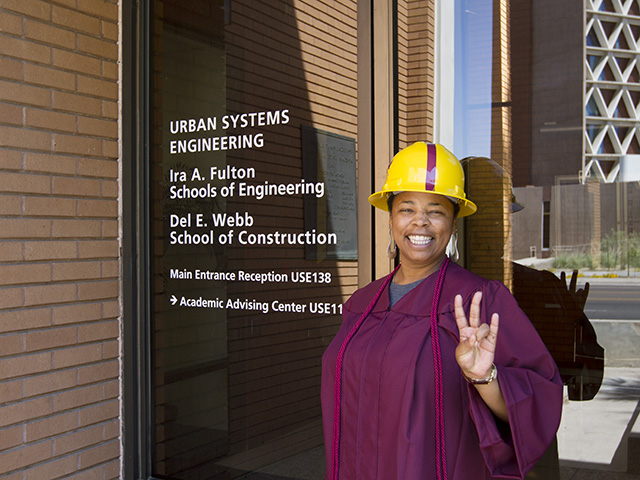
The Waste Management Company of Pen Argyl, a newly opened Federally-funded waste management business in Northampton County, is the Waste Management Company of Pen Argyl. This facility will provide 126 new jobs and help the community in several ways. Federal Matching Grants are one example. This grant is designed to help local governments and businesses attract new jobs and businesses.
126 jobs
The proposed expansion of a waste management landfill in Pen Argyl is creating 126 new jobs, including overtime. The proposed landfill is estimated to provide a $4 million annual benefit to the town and supports a variety of local businesses and initiatives. You may also have the option of overtime which could raise a person’s salary to six figures.
This expansion is part of a bigger plan to reduce landfill costs. It also includes reducing emissions and creating jobs. Plainfield's company offers free trash pickup, recycling, support for the Wind Gap Ambulance Corps, as well as habitat for wildlife. The community is charged a $2.2 million host fee, which amounts to $1,042 per household. This host fee will decrease to zero if the landfill is closed.
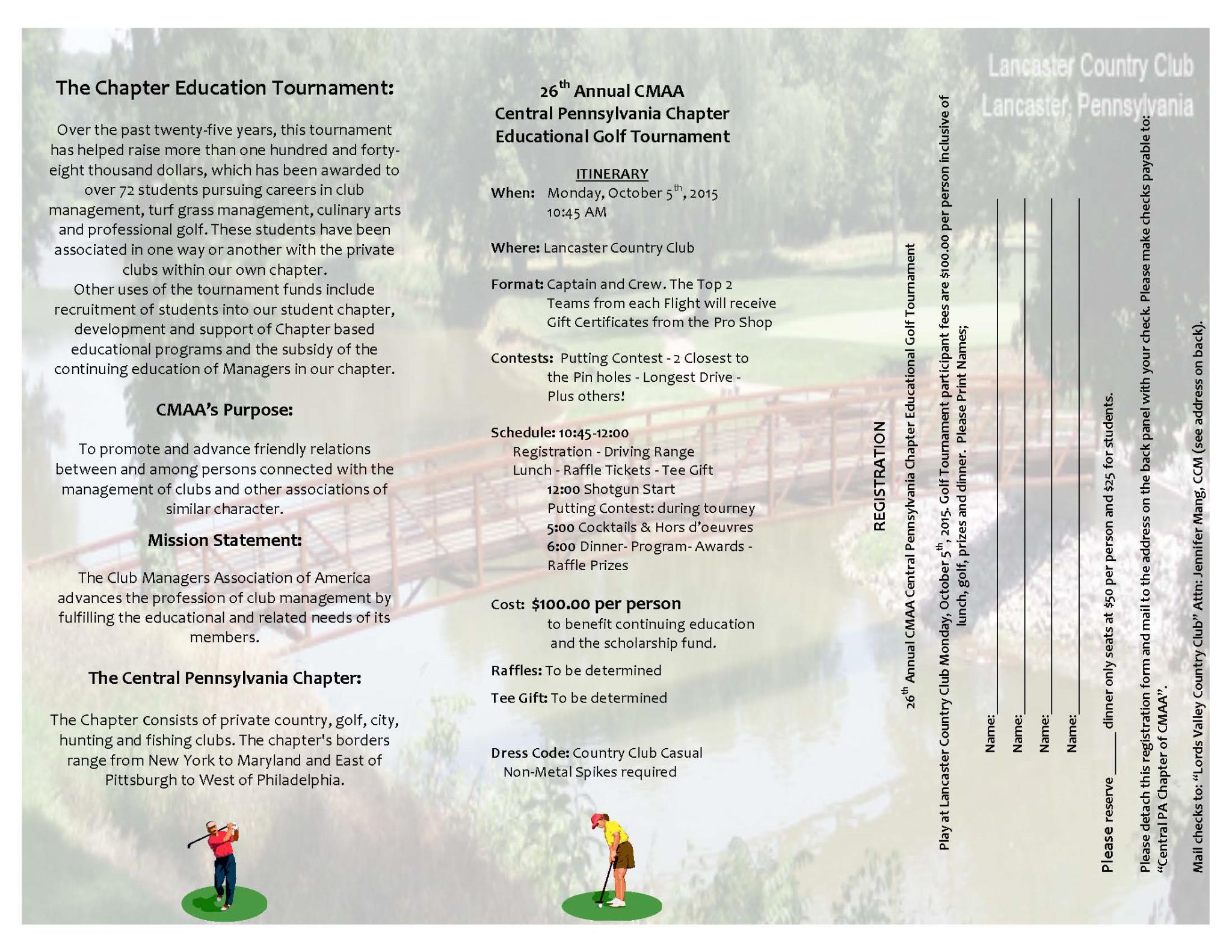
Federally funded
The Federally funded waste management program Pen Argyl in Pennsylvania dates back to the 1930s. It is a success story that has helped local governments manage their waste while also creating jobs for residents. President Clinton initiated the program. It continues to operate today. Two borough police officers are paid a small amount of the grant.
The landfill has been a major source of revenue for the local community, with a tax rate of 1 mill a year. For the average homeowner, that's roughly $50 per annum. The town also receives $250,000 per year from Green Knight, a green energy company that burns landfill methane. Waste Management offers $150,000, and the township recently demolished the Bet building.
Northampton County
Northampton County has upgraded its solid waste collection and recycling facilities. The county maintains manned recycling stations for glass and paper as well as aluminum. It also accepts food and beverage cartons and waste oil. Special Olympics Virginia is also a partner in providing clothing collection bins for waste collection centers.
Northampton County Waste Management officials are seeking input on a proposed expansion for the Grand Central Sanitary Landfill. The owners of the landfill are planning to double its size. They invite residents to attend an information session. The company plans to increase the solid waste zoning area by 211 acres. The landfill currently has a daily limit of 2,750 tonnes. The landfill is expanding to increase its daily volume to 5,000 tonnes per day. It will also provide additional land for support activities, and create a buffer area around it.
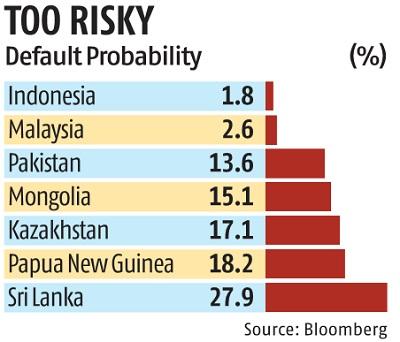
Matching grant
The Department of Conservation and Natural Resources granted $19,500 to Pen Argyl to fund a master site plan. This grant will fund materials and installation of new equipment. It must be matched by a $19,500 contribution from the local community. The Borough thanks Pen Argyl Senior Women's Club, Waste Management, Pen Argyl Area Concerned Citizens, Waste Management and Park Pals for their support.
FAQ
Six Sigma is so well-known.
Six Sigma can be implemented quickly and produce impressive results. Six Sigma also gives companies a framework for measuring improvement and helps them focus on what is most important.
What are the most important management skills?
Business owners need to have management skills, no matter how small or large they may be. They include the ability to manage people, finances, resources, time, and space, as well as other factors.
You will need management skills to set goals and objectives, plan strategies, motivate employees, resolve problems, create policies and procedures, and manage change.
As you can see, there are many managerial responsibilities!
Why is it so important for companies that they use project management techniques
Project management techniques are used in order to ensure projects run smoothly, and that deadlines are met.
Because most businesses depend heavily on project work to produce goods or services,
Companies must manage these projects effectively and efficiently.
Companies can lose time, money, and reputation if they don't have a good project management system.
How can a manager motivate his/her staff?
Motivation is the desire for success.
It is possible to be motivated by doing something you enjoy.
You can also get motivated by seeing your contribution to the success or the improvement of the organization.
For example, if your goal is to become a physician, you will probably find it more motivational to see patients rather than to read a lot of medicine books.
The inner motivation is another type.
You may feel strongly that you are responsible to help others.
You may even find it enjoyable to work hard.
If you don't feel motivated, ask yourself why.
You can then think of ways to improve your motivation.
Statistics
- 100% of the courses are offered online, and no campus visits are required — a big time-saver for you. (online.uc.edu)
- UpCounsel accepts only the top 5 percent of lawyers on its site. (upcounsel.com)
- The BLS says that financial services jobs like banking are expected to grow 4% by 2030, about as fast as the national average. (wgu.edu)
- Your choice in Step 5 may very likely be the same or similar to the alternative you placed at the top of your list at the end of Step 4. (umassd.edu)
- Hire the top business lawyers and save up to 60% on legal fees (upcounsel.com)
External Links
How To
How do you apply the Kaizen method to your life?
Kaizen means continuous improvement. This term was first used by Toyota Motor Corporation in the 1950s. It refers to the Japanese philosophy that emphasizes continuous improvement through small incremental changes. It is a process where people come together to improve their processes.
Kaizen, a Lean Manufacturing method, is one of its most powerful. Employees responsible for the production line should identify potential problems in the manufacturing process and work together to resolve them. This improves the quality of products, while reducing the cost.
Kaizen is about making everyone aware of the world around them. To prevent problems from happening, any problem should be addressed immediately. If someone is aware of a problem at work, he/she should inform his/her manager immediately.
Kaizen follows a set of principles. The end product is always our starting point and we work toward the beginning. For example, if we want to improve our factory, we first fix the machines that produce the final product. We then fix the machines producing components, and the machines producing raw materials. And finally, we fix the workers who work directly with those machines.
This is why it's called "kaizen" because it works step-by-step to improve everything. Once we have finished fixing the factory, we return to the beginning and work until perfection.
It is important to understand how to measure the effectiveness and implementation of kaizen in your company. There are several ways to determine whether kaizen is working well. Another method is to see how many defects are found on the products. Another method is to determine how much productivity has improved since the implementation of kaizen.
If you want to find out if your kaizen is actually working, ask yourself why. Did you do it because it was legal or to save money? Did you really believe it would lead to success?
Let's say you answered yes or all of these questions. Congratulations! You are ready to start kaizen.